Home Products: R-Hauz, Toronto, Ontario and Intelligent City, Vancouver, British Columbia
TEXT Elsa Lam
Construction is a field ripe for efficiency improvements: notwithstanding improvements in materials and in building science, a building takes roughly the same amount of time and labour to be built today as it did seventy years ago.
Prefabrication technologies, with their factory precision and production-line efficiency, have long promised to improve things. That promise was realized spectacularly this winter, when a 1,000-bed hospital in Wuhan were constructed in just 10 days on-site.
Canadian architects and designers have also been realizing the potential of prefab construction beyond the scale of modular homes. Potentially, some of the most impactful work is in mid-rise, infill housing—the “missing middle” that is considered crucial for densifying Canada’s cities. Bringing mass timber into the mix—a natural fit, in that mass timber products are fabricated to spec—has the potential to reduce the carbon footprint of the resulting buildings.
In Toronto, a company called R-Hauz is completing a pilot version of a six-storey mass timber townhouse, and will have a pilot version of a two-storey laneway suite under construction this summer. And in Vancouver, Intelligent City has four mass timber projects underway—the tallest two rising to 12 storeys each—which share a common, integrated platform and will be made through an automated, robotically assisted manufacturing process.
R-Hauz
From the beginning, R-Hauz conceived of their townhouse and laneway suite as “repeatable products,” rather than one-offs, according to founding partner Leith Moore, a veteran of the development industry. His team started by developing a site strategy adaptable to a wide number of locations, and designing a structural core that would allow for various unit configurations.
For the townhouse, it’s envisaged that the building would be divided into multiple units, to be either occupied by the owner or leased to commercial and residential tenants. The units use standard bathrooms, prefabricated as modular units. Plumbing and HVAC are also part of the core design, including a greywater recycling system. A green roof, permeable paving, and soaker and tree pits work together to manage storm water on-site.
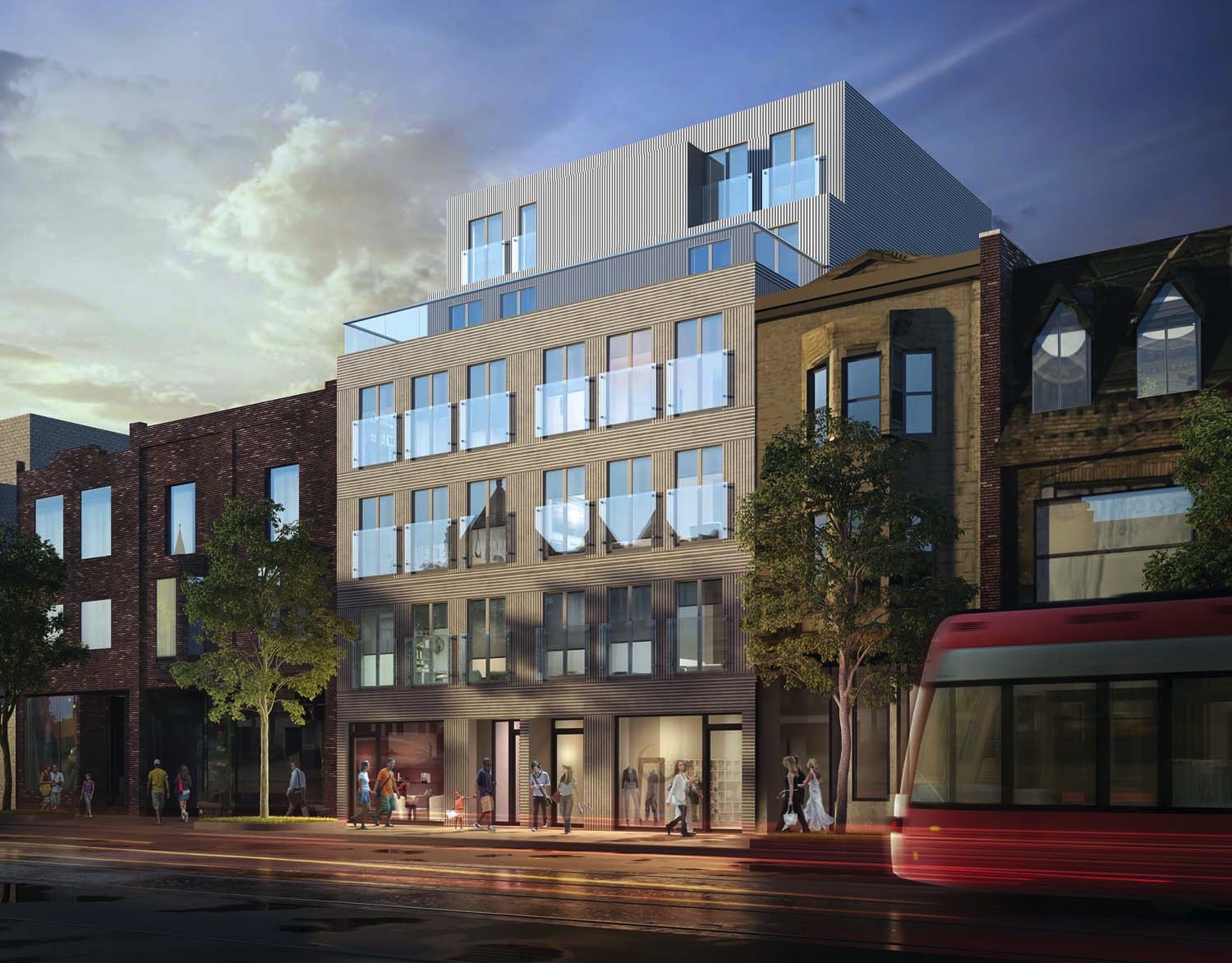
The design is tailored to Toronto’s guidelines for the redevelopment of its many east-west avenues—a set encompassing some 10,000 properties that are well-serviced by transit. Currently, most of these are underdeveloped two- and three-storey buildings, with a storefront at street level and single residence above. R-Hauz’s design packs in more density, hitting the city’s target height of six storeys. The design pulls back on its rear laneway side to allow for soft landscaping and at-grade parking—a move that eliminates the need for a costly underground parking level. The team has also gained approval for a wood circulation core, as an alternative solution to the concrete core that is usually required. As a result, the only poured concrete in the building is a slab on grade, making the building relatively quick and economical to construct.
The complex process of navigating the requirements for that circulation core—as well as a plethora of other details to make the units conform to the municipality’s site plan, zoning, water, and green building standards—is part of a long game, according to Moore. “At the end of the day, we have a package of repeatable solutions,” he says. Crucially, the city has agreed to streamline approvals of R-Hauz’s products, provided the core building and site plan remain the same (the buildings will have varying façades).
At the pilot stage, the construction process is being carefully monitored, in order to seek further efficiencies, which will ultimately help compress the construction timeline. The subconsultants on R-Hauz have signed an Integrated Project Delivery (IPD) contract—a model usually deployed only on larger buildings—that ties the delivery time and cost to financial rewards, incentivizing the team to work collaboratively in optimizing the build. “For me, IPD, pre-fabrication, and mass timber go hand-in-hand,” says Moore.
When the offerings are in full swing, the company anticipates a six-month timeline on the front end of design and municipal approvals, and six months of construction—from pouring the slab to delivering the front door key to the owner. The company’s net-zero-ready laneway houses are targeting a four-week on-site construction period. Moore has been fielding inquiries from private property owners as well as affordable housing providers.

Intelligent City
Can the efficiencies of designing housing as a replicable, pre-fabricated product—and the carbon-sequestering advantages of building with mass timber—be translated into taller buildings with greater variation? A Vancouver group called Intelligent City, led by architect Oliver Lang and designer Cindy Wilson, is doing just that.
Lang and Wilson—who also head a sister company, Lang Wilson Practice in Architecture Culture (LWPAC)—founded Intelligent City in 2008, after building a Vancouver infill project that explored the typology of densified urban living. Completed in 2006, the 1,950-square-metre ROAR_one fills the maximum permissible building volume for its site, and then perforates that space with patios, slotted courtyards, and open-air sky gardens. Each of its ten residential units spans two levels and includes double-storey interior and exterior spaces; the strategic use of aluminum-grate sliding screens and bamboo plantings provides privacy and reduces heat gain.
ROAR_one netted the young designers a Governor General’s Medal in Architecture and became one of the City of Vancouver’s first Passive House reference projects. Says Lang, “it had the DNA for high quality urban housing that prioritized livability, but it was impossible to replicate a building like it and make it scalable.”
Lang and Wilson’s next foray was MONAD—a multi-unit building half the size, but with the ambition to be replicable. It drew on the duo’s longstanding research into parametric software, automation technologies, and advanced building materials.
Completed in 2012, MONAD houses a commercial ground floor with four residential units above, on a 10-metre-wide site—a standard single-family lot size in Vancouver. The main structure was prefabricated in a series of shipping-container-sized modules, which were lifted onto the site in a single weekend.
Today, Intelligent City’s and LWPAC’s shared office is on the ground floor of MONAD, and the couple lives with their two teenage children in a penthouse unit above. On a recent trip to Vancouver, I stayed in their guest room, which doubles as a family room. Despite the unit being just over 150 square metres in size, its careful planning, natural light, double-height spaces and expansive views made its rooms feel generous—more like a modernist single-detached home than a typical, shoebox-tight condo.
At the time, wrote architecture critic Adele Weder, MONAD’s idea of mass customization made it a “rarified design.” But it may simply have been ahead of its time. Fast-forward eight years, and Intelligent City is realizing its original mission—of making high-quality urban housing replicable, scalable and adaptable.
“From the beginning, we asked, how could we bring the qualitative aspects of MONAD to far more people?” says Lang. Intelligent City’s answer is a prefabricated mass timber housing system called Platforms for Life that can be configured and customized in myriad ways, and that targets carbon neutrality.
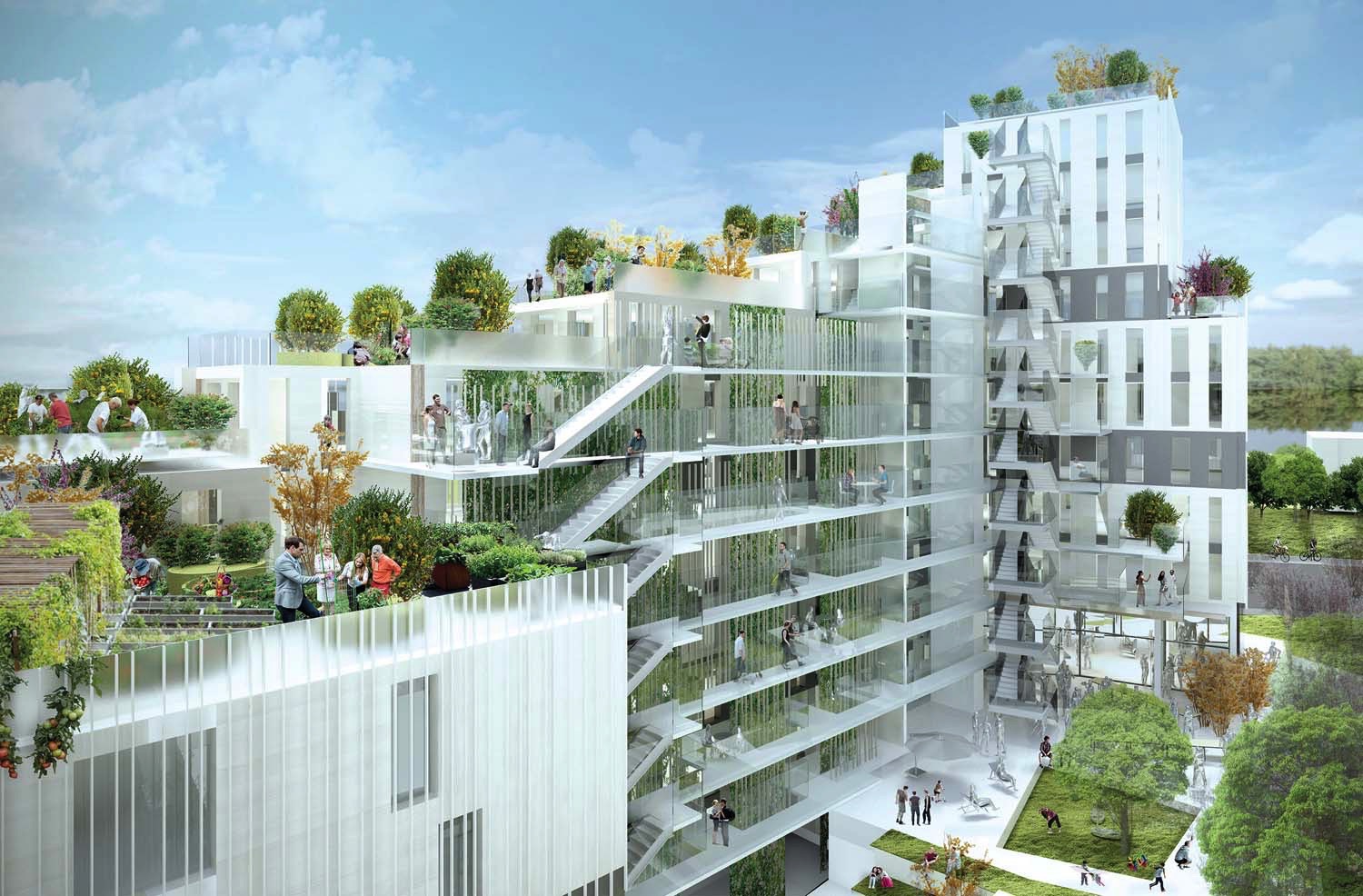
Like R-Hauz, Platforms for Life sees housing as a product, rather than the result of one-off design. A common design and technology platform—a kind of DNA that can be repeated between buildings—includes a patent-pending mass timber structural floor panel system that integrates various building systems, and a fully integrated Passive House façade. (According to Lang, this platform gives Intelligent City’s four active projects 80 percent of the same construction systems and building products).
An urban home—which enjoys the same kind of slot courtyards and multi-directional views developed for ROAR_one and MONAD—is made up of three to four floor panels. These homes can be grouped and configured in many different ways. The platform-based approach means that the resulting buildings can be adapted over time, for instance, to suit shifting family configurations or changing societal needs. Structural systems have been engineered to support a building up to 18 storeys in height.

Lang and Wilson foresee that design-engineering, supply chain integration, and manufacturing efficiencies, along with the predictable costing of prefab, will make the units substantially more affordable than current housing in Vancouver. “Our industry is centred on the costing of projects, and today, that’s based on the exploitation of loopholes in contracts,” says Wilson. “The net result is that projects are more expensive than they should be, and not as good as they can be.”
In Intelligent City’s model, the potential efficiencies extend from the beginnings of the design process through to construction. The practice’s team has developed generative design software that explores multiple scenarios for any given site, reduces the time needed for developing construction drawings, and communicates directly with CNC and robotic fabrication equipment. They’ve designed a highly automated manufacturing facility, which they modelled virtually to maximize spatial efficiencies. They’re currently writing the machine code for its robotic systems. The fully equipped factory is expected to open this summer.


The approach is already seeing significant success. Two projects based on the platform—the four-storey Monad_Rupert and 12-storey Corvette Landing—received a 2017 LafargeHolcim North America Award in their design phase. Both buildings start construction this summer. Corvette Landing was one of 11 projects selected in the CleanBC Better Buildings competition for net-zero energy-ready buildings.
Last October, Intelligent City was selected as a prioritized proponent for the CMHC’s Affordable Housing Innovation Fund, which would provide a full financing package to see its four present projects through to completion. And in February, the platform was one of ten winners in the national Breakthrough Energy Solutions Canada Initiative, a public-private effort to accelerate the development of scalable clean energy technologies. The win comes with $3 million in R&D funds, adding to some $3.1 million in private financing that Intelligent City secured last fall.

Traditionally, prefabrication is based on creating a uniform, standardized product. Lang says that their approach is fundamentally different. “From the beginning, our platforms were designed to be as adaptable as possible,” he says. Even with MONAD, they considered how the design could scale up to a 17-storey-building and be brought to a higher level of environmental performance.
When they began their research fifteen years ago, mass timber was just emerging on the market, but Lang and Wilson anticipated that it would be the ideal material for their vision of replicable, high-quality urban housing. They appreciated the precision and consistency with which it can be manufactured, particularly using automated, robotic machinery. Wood’s ability to sequester carbon allows Intelligent City’s buildings to target net-zero carbon.
Being active in national and provincial committees to review and regulate the use of mass timber was part of the long timeframe of advancing the project. Now, with building codes permitting 12-storey mass timber unfolding throughout Western Canada and the northwestern States, the ground is ripe for rapid advancement. “There’s the possibility that we could start manufacturing from Alberta down to Oregon,” says Lang. “That’s an incredible opportunity to build an industry.”
The future–of architecture?
The clean tech sector rarely talks about buildings. And yet, they’re responsible for 40 percent of global GHG emissions. These emissions must decrease rapidly to stabilize the climate.
For designers like Lang, Wilson, and Moore, new models for implementing change must take hold. “Most of the time, architects are still building custom homes like artisans,” says Wilson. “We can’t implement innovation since it’s impossible on the individual level of the building.” She adds, “For us, the motivation is that we want to get to better buildings—not just for a few, but as an industry.”
At present, the pinnacle of an architect’s career is the prospect of creating a landmark building—a showcase museum, a concert hall. But with the starchitect era on the wane, one can imagine this ideal shifting towards a goal of enacting systemic change. “What is the ability of the architect to make a deeper contribution? What if we could really use the power of industry and technology 3.0 to change buildings, so that they’re not like making one custom suit at a time, but so that they can have a larger impact on society?” asks Lang.
“Think 2050—can you imagine that we are still building cars with internal combustion engines?” says Lang. “Can we imagine that we still construct buildings as one-offs with manual labour? That we create buildings that are not based on renewable materials, that are not carbon neutral and resilient?” He adds: “30 years may seem like an eternity in other industries, but in construction, that is the day after tomorrow.”
Did you find this article helpful? Please consider signing up for Canadian Architect’s FREE digital edition and weekly e-newsletter. Your support is a big help to us, as we work to continue reaching readers during this challenging time.