Raising the Bar: Ken Soble Tower, Hamilton, Ontario
North America’s first EnerPHit-standard retrofit of a housing tower brings greater energy performance, comfort, and resilience to 146 affordable seniors’ apartments.
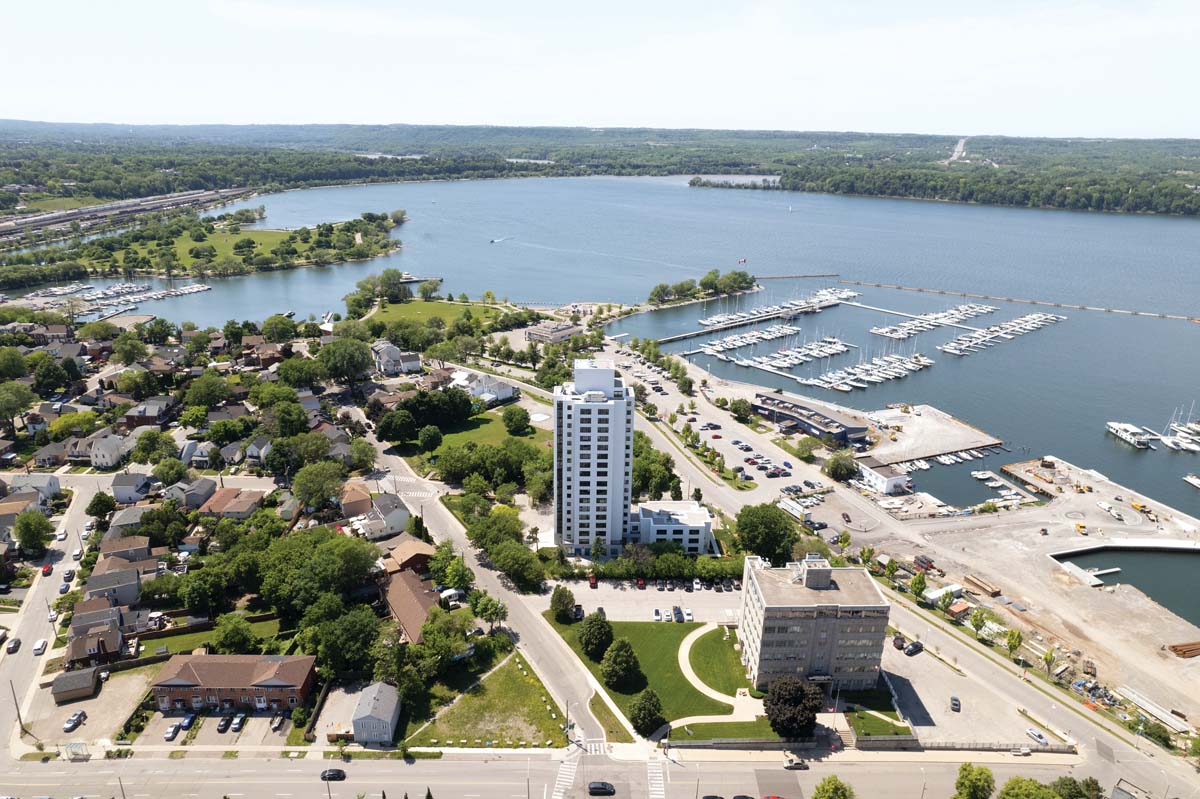
PROJECT Ken Soble Tower, Hamilton, Ontario
ARCHITECT ERA Architects Inc.
As the effects of the climate crisis take hold, it is increasingly clear that to be good architecture, buildings must be sustainable. Conversely, even buildings that meet the highest standard of sustainability must be well-designed to be considered successful.
There is a massive balancing act required between these two value systems. That balance is affected by numerous factors—including the dire need to achieve zero carbon in our buildings now, and the need to design the best possible architecture for people and communities. In other words, we must design for both the environment and for people.
The Passive House EnerPHit certification—a version of the Passive House standard, adapted for retrofits—combines both of these considerations. It is the highest voluntary standard of building retrofit design, providing a science-based methodology that lays down specific human-focused functional requirements. EnerPHit buildings provide for high levels of health, comfort, durability, resiliency against climate extremes and disease, and energy efficiency.
EnerPHit was the methodology of choice for CityHousing Hamilton and ERA Architects, whose recent rehabilitation of an 18-storey, 146-unit seniors’ affordable housing tower has contributed to positioning Hamilton as the leading Passive House municipality in Ontario. It is fascinating that the Ken Soble EnerPHit Tower Retrofit—a first-of-its-kind in North America, as the continent’s largest EnerPHit building and first EnerPHit high-rise apartment—has happened in Hamilton, and not in Toronto, Montreal, Vancouver or even in New York or Chicago.
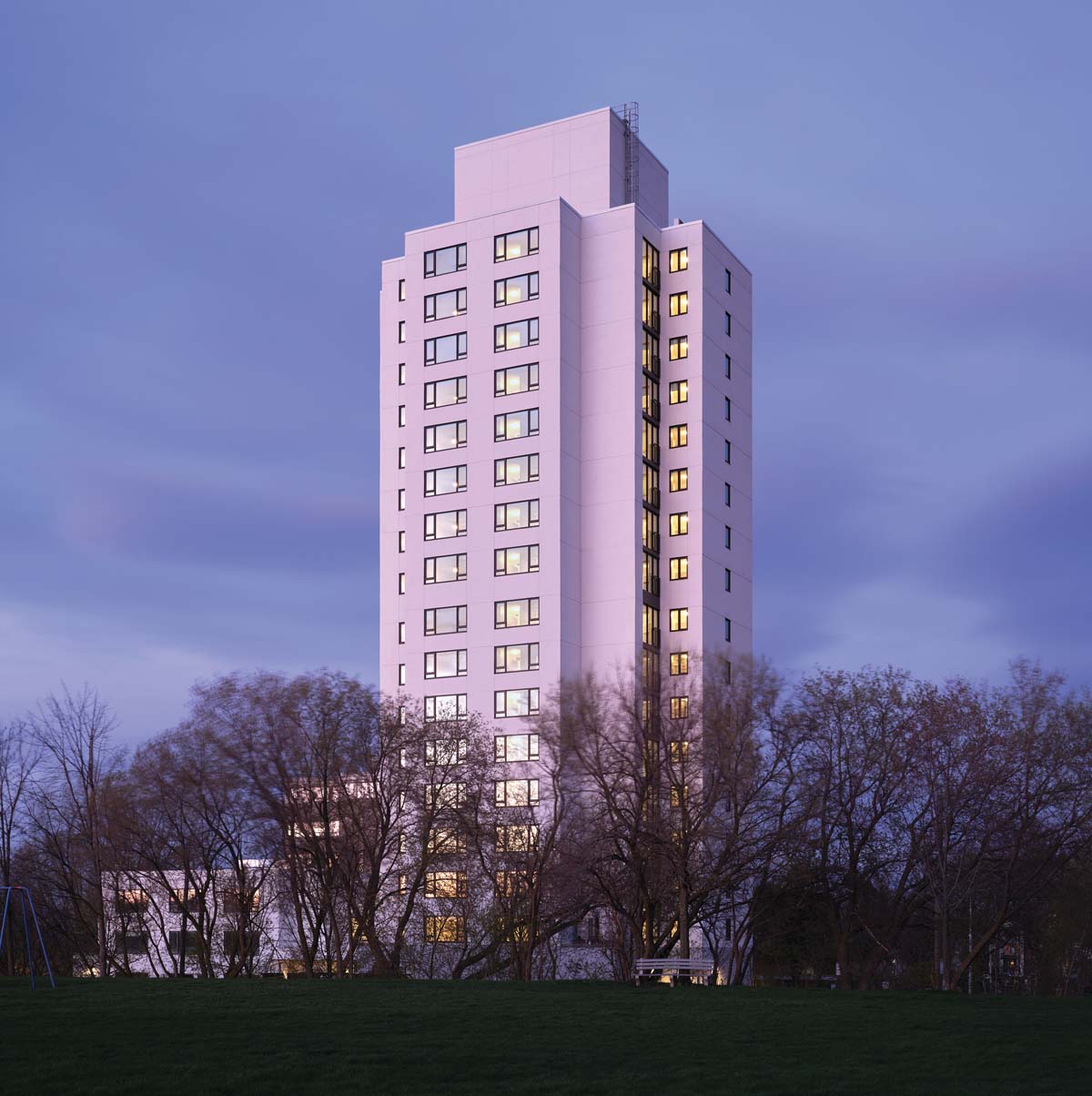
The Ken Soble project is being proffered as a prototype for the renewal of Ontario’s extensive stock of aging residential towers—there are some 2,000 similar concrete towers in the Greater Toronto Area alone, with more than a million inhabitants. This vision, advanced by the multi-disciplinary, non-profit Tower Renewal Partnership, proposes not only to carry out energy retrofits to these buildings that are critical to our housing stock and energy ledgers, but to make them great places to live for the next 100-plus years.
Many towers lend themselves well to high-performance over-cladding of the building envelope, and to being elevated to a new level of architecture in the process. But for such an outcome, the design and coordination process must be envisaged holistically: incorporating both engineered solutions such as improvements in insulation, air tightness, the elimination of thermal bridges, and upgrades to mechanical systems, alongside considerations for human safety, comfort, occupation, and use. The sequencing and phasing of renovations is also critical to achieving the most effective long-term results.
“In the early years of building retrofits, a widespread measure-by-measure approach encouraged owners to undertake improvements to the ‘low-hanging fruit’—the measures with the shortest ROI (return on investment),” says ERA associate and project architect Ya’el Santopinto, who co-led the Ken Soble Tower Retrofit with principal Graeme Stewart, along with a specialized team of retrofit architects at ERA. (Santopinto and Stewart are also key collaborators in the Tower Renewal Partnership.) Unfortunately, says Santopinto, piecemeal upgrades—such as, for instance, replacing inefficient boilers like-for-like—have the unintended consequence of locking in carbon through extensive but ultimately inappropriate renovations. They also eat up funds that could have gone towards more comprehensive future retrofits.
“ERA’s tower renewal approach has always looked at buildings as holistic ecosystems, prioritizing the measures which improve comfort: indoor air quality, thermal comfort, and so on. This points us to an enclosure-first approach, where building systems can subsequently be downsized and ventilation improved,” says Santopinto. “Holistic retrofits always require an architect-led team.”
At Ken Soble, ERA and its team of consultants (including Transsolar, JMV Consulting, and Reinbold Engineering) was faced with a semi-derelict, mould- and pest-infested building. Its mechanical and electrical systems were beyond their end of life. Typical of affordable housing projects, the budget for turning this around was extremely tight. Given these parameters, the completion of the project—and the added achievement of meeting EnerPHit metrics, which entail delivering energy performance up to 85 percent better than conventional builds—is remarkable. The renovated tower achieves a 94 percent reduction in greenhouse gas emissions, and an 89 percent reduction in thermal energy demand intensity (TEDI).
The project is an outstanding example of balancing scope, cost, quality and schedule to turn a nearly 55-year-old building into vital, fresh, and healthy new accommodation for seniors in 2021. “Giving the Ken Soble tower a second life as a critical part of the affordable housing system in Hamilton is, for ERA, the biggest success of the project,” says Santopinto.
To the casual observer, the 1960s-era building has not changed significantly: it lost its balconies and the texture of its brick cladding, interspersed with exposed horizontal concrete slab edges. It received a new overcoat of air-seal, insulation and stucco combined with triple-glazed fibreglass windows. Indoors, there are more visible changes: each unit received new kitchens, bathrooms, flooring and lighting. One of every five units was upgraded to be barrier-free. The penthouse laundry room was re-imagined as a solarium, and a new ground-floor laundry room and community room connect to an outdoor terrace and garden. But the differences go far deeper: the Ken Soble Tower is now a very different animal than before, with very low energy consumption and a high level of interior comfort and health for its resident seniors.
One of the key principles of Passive House design is to create a tight building envelope, free of thermal bridges. An early decision was to remove the building’s balconies, which did not meet accessibility standards and were a major source of thermal bridging. They were replaced with Juliet balconies and full door-sized casement windows, which allow for cross-ventilation during the shoulder months. Other thermal bridges were addressed by surrounding the foundation with concrete-board-faced XPS, and retrofitting the sanitary stacks with a negative-pressure-activated vent that automatically closes when the plumbing is not in use. The wall assembly was retrofitted with an exterior EIFS system, including some 10 inches of rigid mineral wool.
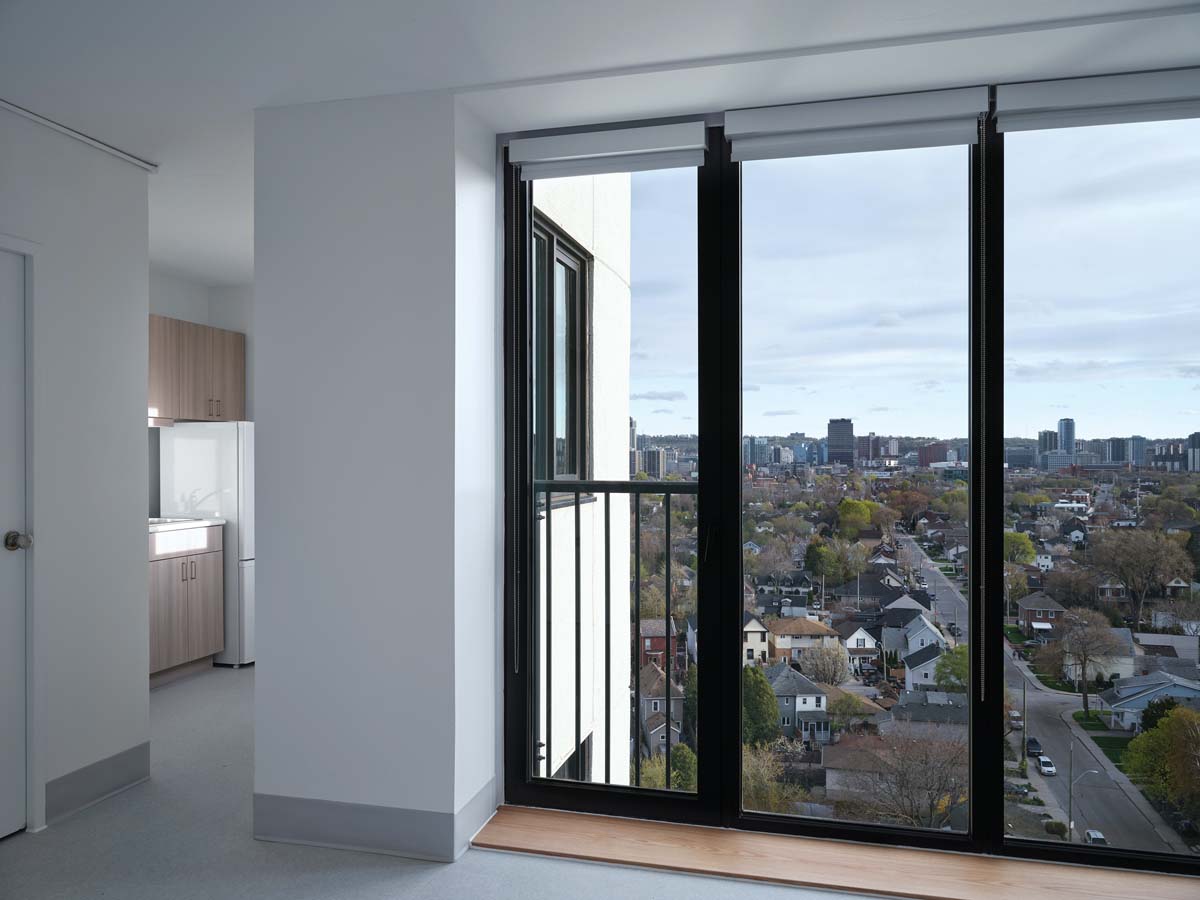
The high-performance building envelope does much to improve residents’ comfort and safety. It effectively eliminates drafts. It also enhances acoustics and prevents condensation and mould. As a result, relative humidity can be maintained year-round at a comfortable and pandemic-resistant level of approximately 50 percent, without risk of damage to the building fabric. (Airborne pathogens, also known as aerosols, travel less easily when the relatively humidity is between 40 and 60 percent.)
The building’s HVAC systems are seen holistically, and include a Canadian-made, Passive House-certified Energy Recovery Unit, a centralized heat pump, new ductwork, interior ceiling fans, Canadian-made Passive House-certified fibreglass windows, and interior shades. These work together to provide constant fresh air, keeping the tower cool in the summer and warm in the winter. Because the systems consume little energy, the tower has a built-in ability to better withstand extreme climate events such as heat waves.
Before the renovation, the tower’s HVAC system only provided air to the corridors, and pressure differentials drove air into the apartments—a solution common for post-war housing towers. As part of the retrofit, the building’s ductwork was modified to afford fresh air directly to the suites, and the original semi-centralized system was also resized accordingly. Providing air directly to the suites ensures the high quality, clean, fresh air required by the Passive House Standard, while also making the building pandemic-resilient—something most of us would never have thought necessary to consider two years ago.
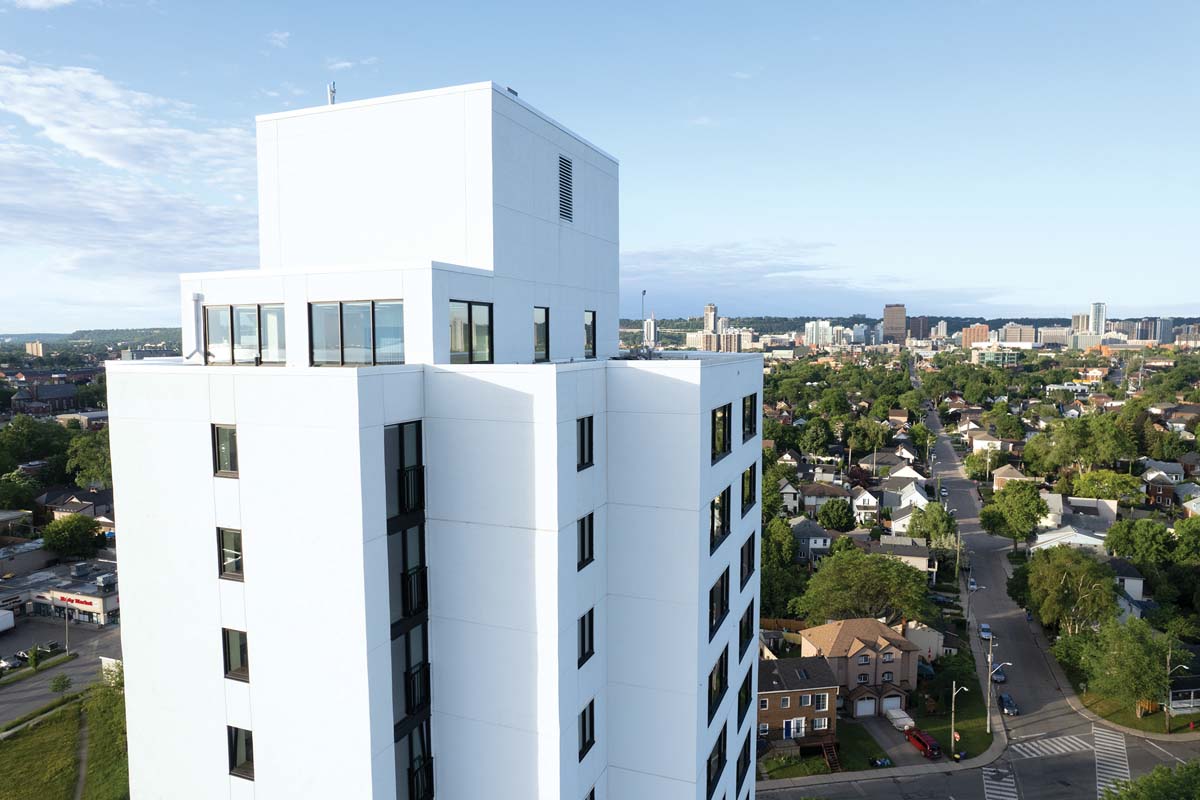
The ERA team spent time investigating the best, simplest and most error-proof envelope solution using readily available materials that could meet the EnerPHit requirements. Typically, that entails increasing the wall thickness substantially—sometimes up to half a metre deep, most of which is insulation. The original plan was to retrofit the entire envelope from the exterior, but then, black mould was discovered on the interior drywall. The revised plans included adding mineral wool insulation to the interior of the exterior walls, and applying an exterior EIFS solution that was less deep—150 mm instead of 250 mm—creating a more typical detail for the trades.
Cap pieces for the exterior insulation still needed to be custom-made for this project, but subsequently they have become readily available to market. This highlights how a single building can change our supply chain and our access to quality materials.
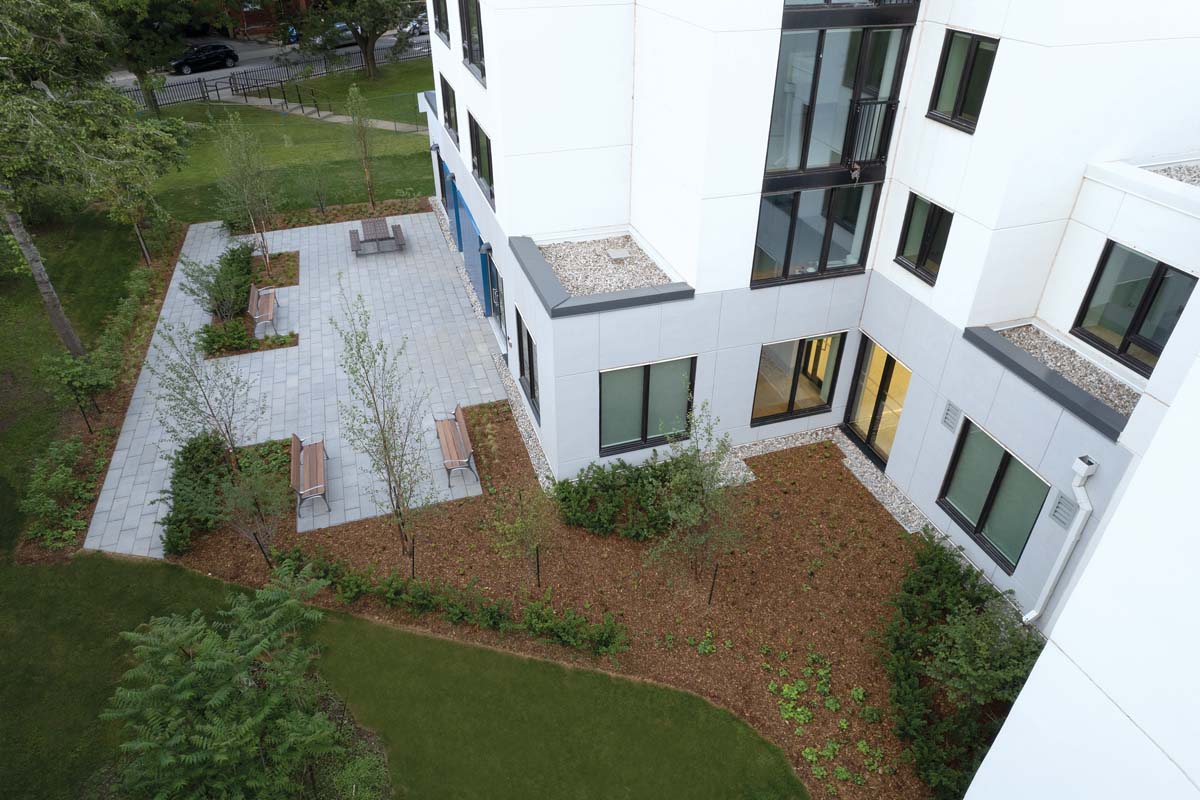
Window installations also needed to be thermally broken. The windows sit outboard of the wall, strapped back to the brick, and rest on fibreglass angles. They are completely surrounded by mineral wool insulation. Silicone air barriers were used instead of tapes to maintain the requirement of user-friendly installation, and to reduce the risk of taping failure—and subsequent problems with air tightness.
There is little new here—but achieving Passive House standards entails rock-solid specs and an expectation for a higher quality standard of build. And while there are some examples in Europe where larger budgets enabled EnerPHit renovations with major changes to the building’s architecture, such changes are merely icing on the cake. These additions were not needed or warranted in the case of the Ken Soble Tower. The achievement of EnerPHit standards provides a sense of wellness and calm to its interior spaces—attributes that are not automatically afforded by other design extravagances.
Notably, attaining EnerPHit performance levels was not a major cost driver for the project. ERA reported that 80 percent of the project’s costs went to capital repair work—including base building repairs, mould and asbestos abatement, accessibility upgrades, and interior fit-out. Only 20 percent went to energy efficiency and systems upgrades. Overall, ERA estimates that the added cost for Passive House-specific measures accounted for about 7.1 percent of the budget. They also recognize that much of this expense was tied to the risks taken on by the contractor, and an inherent cost of being “first adopters.” As the training of trades turns towards a focus on sustainability, and a mainstream understanding of EnerPHit and Passive House take hold, they anticipate that the perception of risk will greatly decrease.
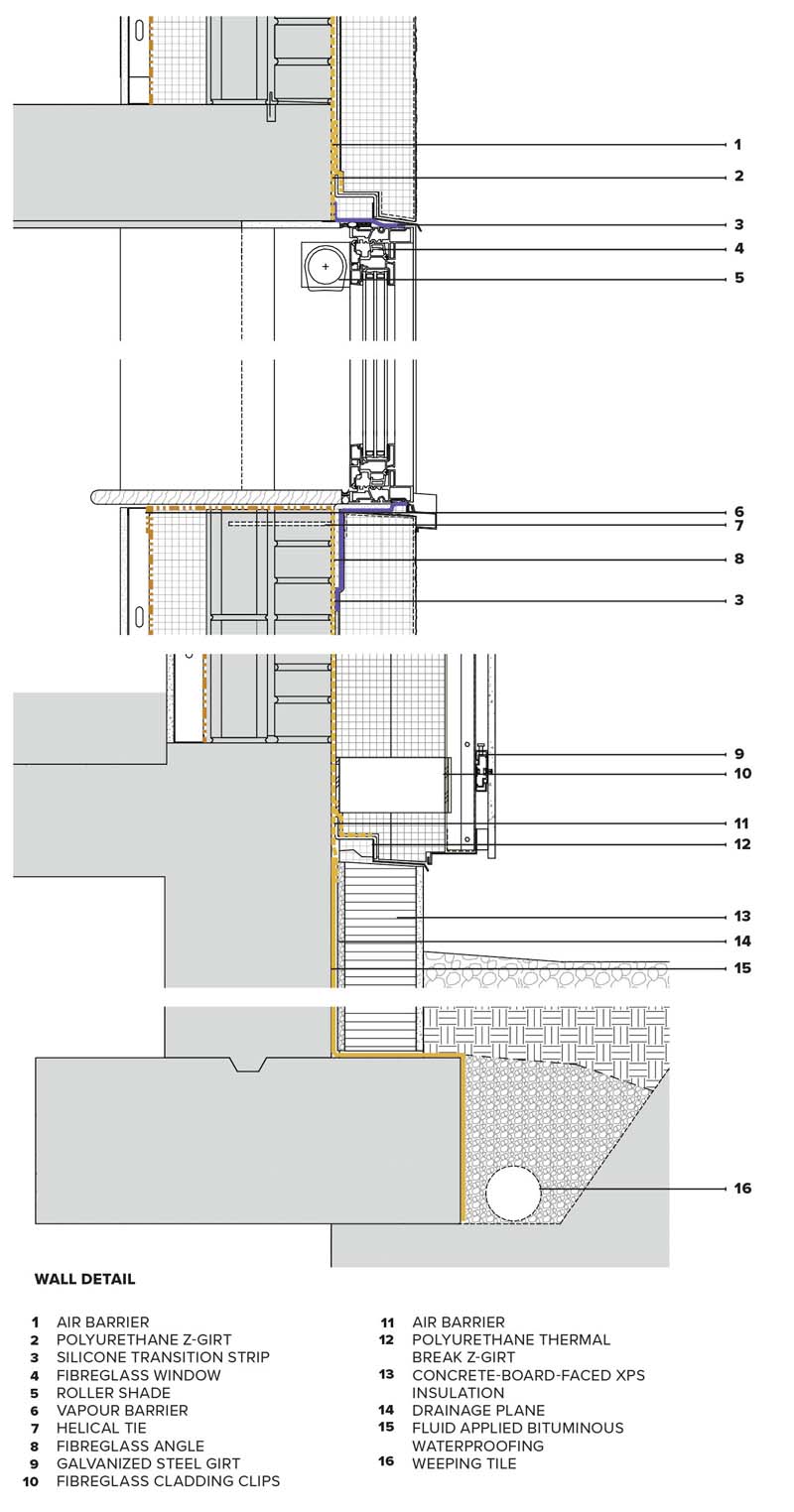
“In the absence of clear guidance for retrofit standards, EnerPHit provides the best path forward—in terms of energy and GHG emissions, but also health and comfort,” says ERA principal Graeme Stewart. “Modifications to address micro-challenges in the Canadian context aside, we would certainly advocate for this as a benchmark to strive toward, and recommend several more showcase projects to further kickstart industry readiness.”
The client for the project agrees. “CityHousing Hamilton has demonstrated that comprehensive modernization of aging housing stock is viable through a holistic approach to deferred maintenance, which can unlock funding-enabled measures when guided by a human-centred design standard like EnerPHit,” says Sean Botham, the development lead for the municipal affordable and social housing provider.
It’s conceivable—and would be desirable—for EnerPHit to be applied to all of Ontario’s similarly constructed housing towers. In the long term, such retrofits make financial and environmental sense: many of these buildings are nearing the end of their lifespan, and normally, a renovation will cost a lot less than demolishing and rebuilding, not to mention saving vast amounts of energy and carbon.
But owners of these towers are often slow to better their buildings. There must be ongoing motivation for the municipalities and private sector players who own these buildings to undertake such retrofits. Could such projects be supported by tax incentives, green mortgages or low-interest loans?
Needless to say, the occupancy, structure and condition of any particular building will determine its feasibility for an EnerPHit retrofit. There are also other technical hurdles to consider. Ken Soble was vacant for the duration of the retrofit, but that is most often not the case for residential towers needing retrofitting. The Tower Renewal Partnership has published a Field Guide to completing similar retrofits with residents in situ, and there are numerous examples of Passive House retrofits in Europe where tenants were actively involved in the design and continued occupying their units during construction. The most successful of these have required a very high level of tenant engagement, combined with an extensive use of prefabricated and modular components to reduce the time of construction and inconvenience to tenants, while also enhancing the quality of the building envelope. Keeping most of the retrofit work to the exterior of the building also greatly assists in allowing for continuous occupation.
The success of the Ken Soble Tower pilot project demonstrates that it is financially feasible and carbon-efficient to repair our country’s aging housing towers. Investment and funding in renovating these towers needs to happen urgently. We don’t need IPCC reports to tell us that our climate is currently in crisis, nor do we need special research to tell us that the current Net Zero targets are coming too late. Ken Soble is intended to show owners, asset managers and government bodies what can be done, and what it takes to do it.
One hopes that the Ken Soble Tower Retrofit may also shift the conversation from ROI to a broader perspective on what architecture can do. Project improvements of this scale will rarely pay for themselves in the short term, especially at a time when fossil fuel energy remains relatively inexpensive. This could begin to change as society undertakes a needed shift towards clean energy and carbon pricing, and invests in the preservation of aging housing. Meanwhile, the rehabilitated Ken Soble Tower is having an immediate, and perhaps even more significant, effect: it’s providing its occupants with a safe, secure, comfortable, healthy and resilient place to live. That’s something we all need and deserve.
Deborah Byrne is COO and Director of Passive House Design at Kearns Mancini Architects. The firm has been working on Passive House since 2009, and is an advocate for its use as the basis of design for all high-performance buildings.
CLIENT CITYHOUSING HAMILTON | ARCHITECT TEAM GRAEME STEWART (FRAIC), YA’EL SANTOPINTO (FRAIC), MIKAEL SYDOR (MRAIC), CAROLINA STREBER (MRAIC), RUI FELIX, LEAH GIBLING, DANIELLE MCINTYRE, ABBI KUSCH, LAUREN MARSHALL | STRUCTURAL ENTUITIVE CORPORATION | MECHANICAL REINBOLD ENGINEERING GROUP | ELECTRICAL NEMETZ (S/A) AND ASSOCIATES LTD. | LANDSCAPE ERA ARCHITECTS INC. | INTERIORS ERA ARCHITECTS INC. | CONTRACTOR PCL CONSTRUCTION | PASSIVE HOUSE CONSULTANT JMV CONSULTING | THIRD-PARTY PASSIVE HOUSE CERTIFIER HERZ & LANG GMBH | ENVELOPE ENTUITIVE CORPORATION | ELEVATOR SOBERMAN ENGINEERING | CODE LMDG BUILDING CODE CONSULTANTS | COMMISSIONING CFMS WEST CONSULTING | HAZARDOUS MATERIALS PINCHIN LIMITED | SECURITY/TELECOMMUNICATIONS ZEROBIT1 | CONSTRUCTION CONSULTANT SCR CONSULTING | AREA 7,698 M2 | BUDGET WITHHELD | COMPLETION JUNE 2021
ENERGY USE INTENSITY (PROJECTED) 70 KWH/M2/YEAR | THERMAL ENERGY DEMAND INTENSITY (PROJECTED) 23.5 KWH/M2/YEAR