‘Building Innovation’ with Sidewalk Labs’ Karim Khalifa
In December, Google affiliate Sidewalk Labs unveiled its draft master plan for the Quayside neighbourhood in Toronto. Their proposal includes a dozen mass timber towers—some up to 30 storeys high—connected by underground freight and waste tunnels, and flexible podium (or “stoa”) levels. Canadian Architect editor Elsa Lam spoke with Karim Khalifa, Director of Buildings Innovation at Sidewalk Labs, about the architectural details of the proposal. Here are highlights from their conversation:
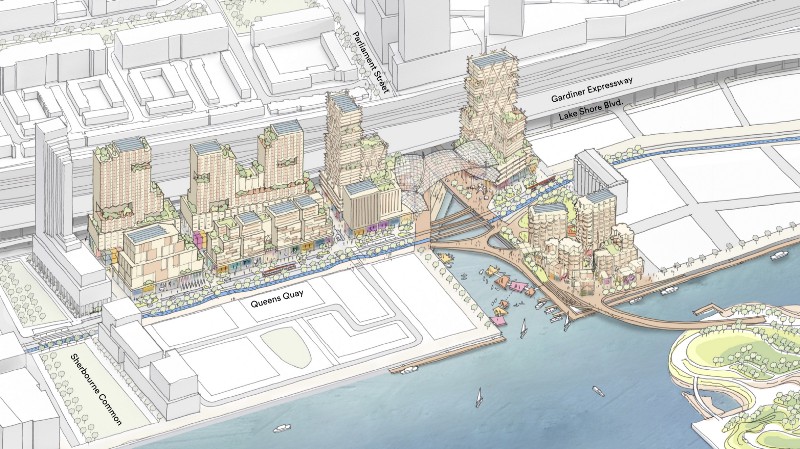
Canadian Architect: I’d like to understand more about are what you’re proposing with mass timber, the concept of the “stoa” on the ground floors, and the underground innovations.
Karim Khalifa: From the beginning, the proposal that Sidewalk put together looked at how to create a really sustainable district. Tall timber was an obvious go-to. Before I joined Sidewalk, I had been doing six to eight storey mass timber buildings in Europe. Here we had the chance to stretch the limits of where tall timber could go.
We got to engage with Michael Green’s office, which had already been exploring taller buildings, and we were able to look at what hybrid elements to introduce to achieve such a height. We asked him to design a kit of parts—what I like to call the library of parts—to build tall timber buildings. And then we tried to make that as efficient as possible. We had two structural engineers on board—one to do it, one to peer review it—and ended up going to the manufacturers of the timber pieces and making sure they felt that all these pieces could be used efficiently. It was a full-industry look at how we could pull this all together.
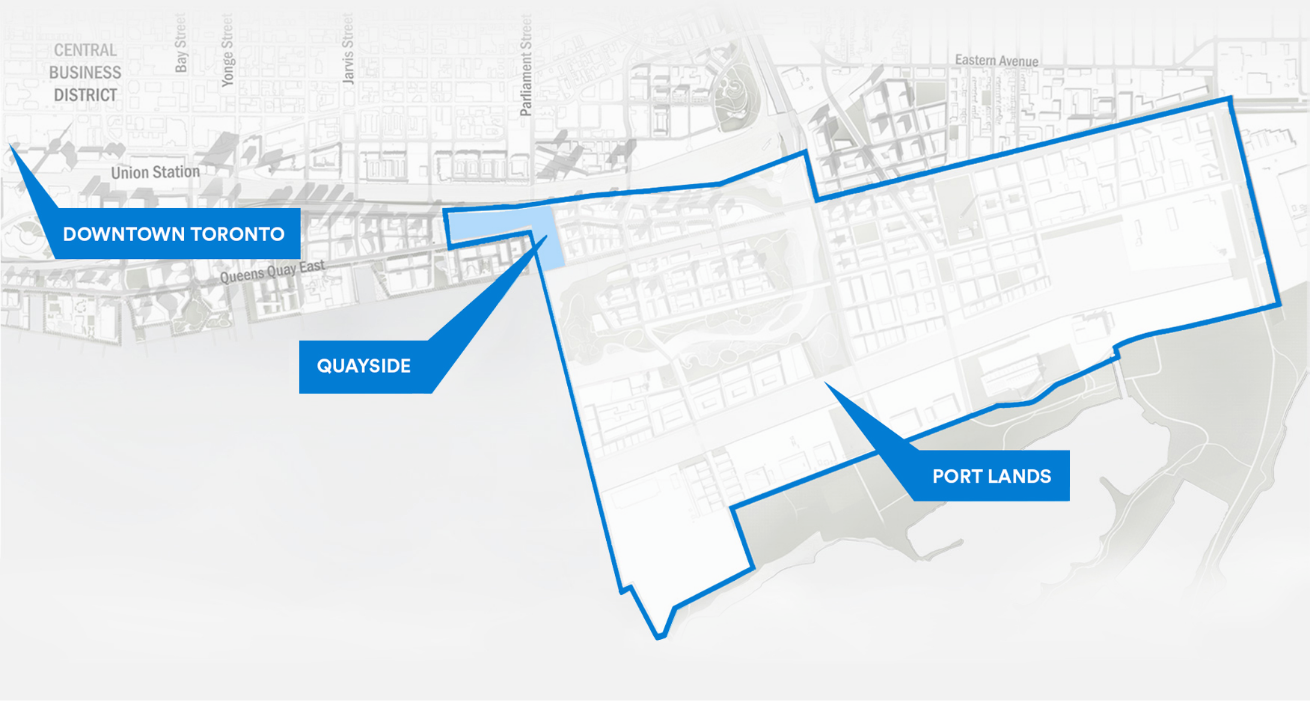
CA: So what is the role of outside architects in this process? It sounds like you’ve been doing a lot of consulting about making this a real proposal, rather than a pie-in-the-sky idea.
KK: Any consultants that we brought in to create the masterplan do not necessarily go forward post-submission and approval of the masterplan. We were able to use some flexibility in who we hired to meet the timelines, to get input from different parties. This is just concept work, which [at] some level [got] quite technical. We would formally bid all this work out to move forward with the actual project.
[After Michael Green produced the kit of parts], we turned it over to other architects and said, “what would you do if we gave you a typical building briefing, but asked you to use this library?” We wanted to see how constraining it was for them, and what faults they might see in this library of parts. We ended up going to Snøhetta and Thomas Heatherwick, and we also asked Michael Green’s office to design one of the buildings. So we had three approaches of using this library of parts. And that’s where we got our submission. It’s been really very fruitful, and the architects gave critiques back to us, which just now we’re incorporating.
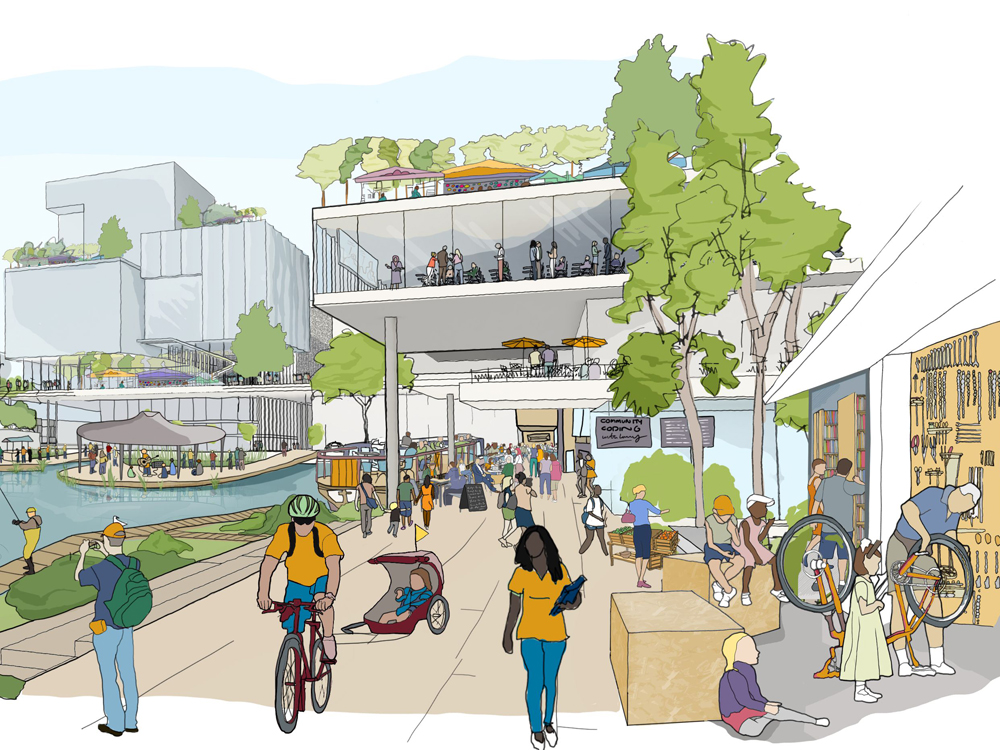
Then we also had three architects from Toronto tell us how they would design dwelling units and condos inside of these buildings. All three of them presented concepts, and we selected gh3* to go forward and integrate those concepts, to start doing more research with residents on how they would react to living in these spaces, which have this wonderful attribute of having exposed timber [surfaces].
CA: You’ve got some nice architects on your roster.
KK: It’s been a pleasure to work with everybody. We had Teeple, Heather Dubbeldam, and gh3* on the apartments, and Michael Green’s office. Structurally, we had Aspect and Equilibrium. So we’ve had some wonderful Canadian architects to work with.
CA: It sounds like you’ve been putting a priority on having Canadian consultants work with you on this.
KK: Look, there’s wonderful talent there. And it’s a Canadian project, so where else should we go? Especially with tall timber, we really want to grow the local talent, so this isn’t just a district, but expands as far as it can across the country.
CA: Are you looking at timber cores of the buildings as well, or more of a hybrid system with parts in concrete or steel?
KK: We [said to] Michael Green, let’s try to be purists and design a timber core. But then let’s also look at concrete and steel. We were able to pick up a master’s student who was studying the manufactured cores of all three materials, from Western University. So he is finishing his thesis, doing this evaluation of which way to go. We think that timber and steel are the most interesting, because their speed is more in rhythm with what we can do with a timber building.
One of the things we imagine is that we can end up with a building configurator, once we know the library of parts we’re going to use. So if we have a five-storey, 35,000-square-foot building and we know the lot lines and setbacks, we can put that data into a digital configurator, and it would tell us all the different types of buildings it can produce to optimize that space. This allows the architect or the developer to have a very quick view of “what could I build here?”, especially using this timber library of parts.
Of course, you would engage with an architect to really make the building beautiful and have meaning. But it’s a quick way to get through that feasibility stage, to understand with some certainty what’s this building is probably going to cost. Then you can make decisions with an architect of what types of customized spaces and components should be introduced. [Since the] architect works with a library of parts, [the configurator] immediately will give them inventory for the cost of those parts and time to produce those parts. So they automatically get a schedule out the back end.
The factory digitally produces those parts, in the exact cuts that were maybe even customized by the architect, and then can ship them to the site. I don’t know how much modular construction you’ve seen, but I’ve worked quite on a few projects, and one of the beautiful things is there’s fewer trucks—maybe a fifth the number of trucks show up at the site—and they don’t need any lay-down space. The crane picks right off the bed of the truck, and puts [the pieces] immediately in place. Digitally, it all started with that configurator—the crane even knows exactly where those pieces go on that day from this digital model. Often they’re able to complete almost a floor a day.
We talk about going beyond that: when that building gets commissioned, all those pieces have been identified and basically have serial numbers, which is so different than construction today. So if there was a problem with some element, you would know where those trees came from, what production line, and look to see if that impact was on any other piece in the building. Today, when you have an issue in a building, everything was custom made or put together on site, so you don’t know if that problem is going to be repeated elsewhere.
CA: That makes a lot of sense. Talk to me about the “stoa”—the strategy you’re proposing for the ground floors of the buildings.
KK: When we use this word “stoa,” of course, most people would use the term “podium.” [We are creating a] ground floor experience of having traditional retail, but also having very flexible spaces to complement that traditional retail. How do we open up those spaces to each other and to the outside, so that we have this very porous environment—with folding garage doors or sliding partitions?
I love old souks, you know, like the markets in Istanbul, where there’s variety [in the vendors]—some are very permanent, some are very temporary. That’s the idea we’re trying to promote. To do so, the first floor is about six metres high. So it allows for a full mezzanine in that space, or two-storey spaces, or someone who can use storage up above. We can have hallways that are quite high and impressive, and have beautiful ventilation.
But we also wanted to make sure that pop-ups could move in easily and be there for a short amount of time, at a very low price point of entry, so we could have more entrepreneurial [tenants] and local craftspeople. We ended up designing a flexible wall system—it’s still being designed—that lets you take partition walls up and down easily. And we enabled that by going to DC power and digital power, which is safe and doesn’t need to run through conduit in the walls. And we [chose] a sprinkler system that runs on tubing versus piping. Although it’s a little more expensive, it also runs on the exterior surfaces of ceilings and walls and can be moved around much more easily. By getting rid of the utilities from within the walls, now the walls can be moved around from place to place to create new environments, especially for that really flexible retail that we’re anticipating attracting.
CA: So the innovations are in how you run the infrastructure to encourage flexibility of use.
KK: We found getting all those utilities [set up] is becoming a barrier to entry. You get the electricians in, and the sprinkler guys in, and before you know it, those walls that really need to pretty simple suddenly got very expensive, and not so flexible. So part of the big push was to simplify [how] infrastructure needs to moved around, to accommodate all these different retail tenants.
CA: You’ll have to help me to understand the digital power.
KK: Power over Ethernet (PoE) gives us about 90 watts on an ethernet cable. But we’ve also looked at digital power which lets us run up to 2,000 watts. This is a new technology – there are tens of buildings out there trying to deploy this. We are trying to deploy it in a very big way. The nice thing about these types of power systems is that they’re non-hazardous – that’s why they’re allowed to run without conduit. One of the side benefits is that we take away a shock source that starts fires. We’ve presented already to the fire department in Toronto, showing them what we’re trying to do to also create a safer space.
It’s a simple wire that looks like a telephone wire. We’re coming up with a system that maybe looks like a baseboard. It can run in the void behind a baseboard along the walls. It can be installed by anybody, by the tenant themselves, and removed when they want to change around the wires.
CA: Tell me about the underground systems that you’re planning to distribute freight and collect waste.
KK: The way Quayside is laid out right now, we have an urban consolidation centre in the northeastern corner of one of the buildings. We’re able to bring in some of the freight and consolidate it into items that can be dispatched into the buildings. The buildings have tunnels connecting them to this urban consolidation centre. Robotic freight can go through the tunnels, get to a freight elevator within a building tower, and put the parcels into the freight elevator in a rack system. Then that rack gets pushed out of the elevator onto a vestibule on a floor. The resident would get a notification and be able to collect their parcel from their own floor.
Likewise, we have a m-vac system to evacuate the waste, but some items don’t fit in there, so on the return trip, some of the freight robots will be collecting boxes and things, and bringing them back to the consolidation centre where they can then shipped to recycling.
CA: And the waste system is a separate set of vacuum tunnels.
KK: As a tenant, I would have a place to go to deposit my waste. It will have organic waste, separated plastics and metals and all those things. Of course, there has to be a good education system. We all get confused because systems are designed differently. We’re going to have [a system] that’s district-wide and we hope broadens further, and helps identify which items go [into which] vacuum tube.
CA: So that sorting is done mostly by the tenants rather than it being an automated system, or it’s a combination of both?
KK: It’s a combination. We’re looking at some automation systems for sorting, using machine-learning to identify the objects that are dropped. There will be details to come on that.
Karim Khalifa is Director of Buildings Innovation at Sidewalk Labs. Interviewer Elsa Lam is the Editor of Canadian Architect.