Modular Solution: Les Pavillons du 49° apartment building, Chibougamau, Quebec
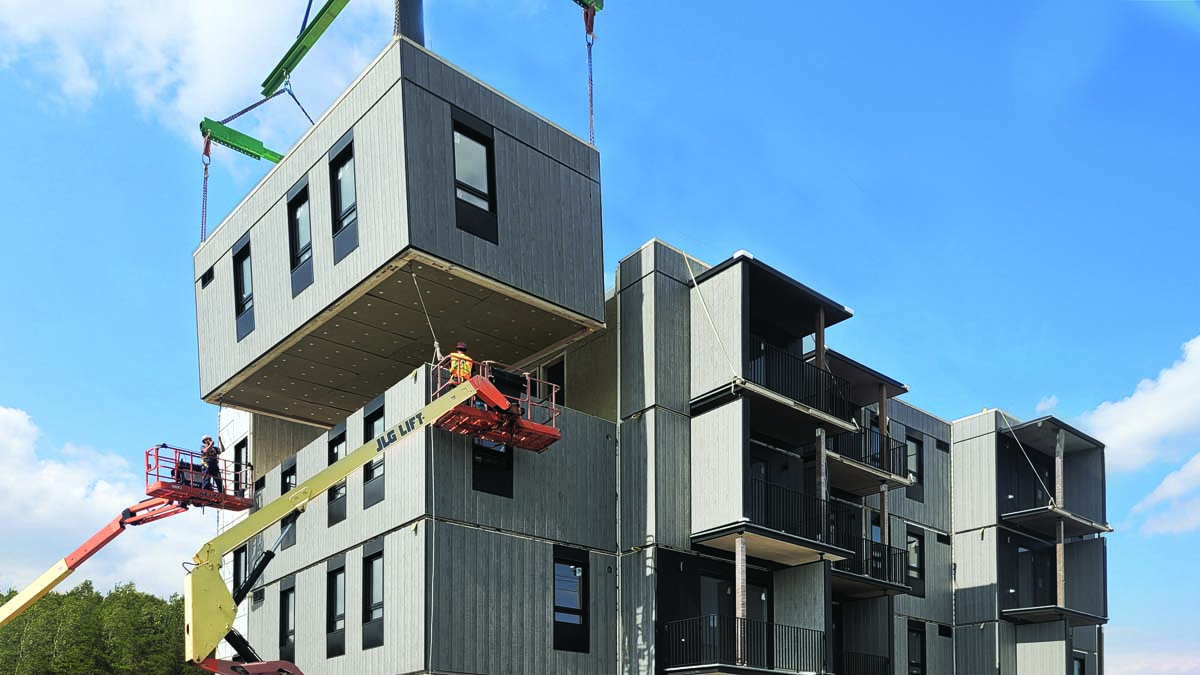
PROJECT Les Pavillons du 49° apartment building, Chibougamau, Quebec
ARCHITECT PERCH architecture
INTERVIEW BY Marco Marini
PHOTOS Ulysse Lemerise, unless otherwise noted
Last summer, one of Quebec’s first mass timber, factory-fabricated modular apartment buildings was built at lightning speed in the city of Chibougamau (population 7,500), a community some 700 kilometres north of Montreal. The four-storey Les Pavillons du 49° apartment complex was constructed from 47 modules, delivered and assembled on site in a mere four days.
The project was spearheaded by Nordic Structures, whose sawmill and production facility is located in Chibougamau, and whose engineered wood products are distributed throughout North America. They worked with Montreal-based studio PERCH architecture, a firm led by architects Suresh Perera and Julie Charbonneau.
The 20 rental units of the building accommodate a varied clientele. It’s anticipated that workers and retirees will live in the building’s studio unit, two accessible units, and five two-bedroom units, while families may rent its dozen three-bedroom units.
It’s only the second mid-rise apartment building in this remote northern town, where the main industries are forestry and mining, and an acute housing shortage leaves many locals living in temporary trailers. This housing shortage is exacerbated by a lack of construction labour, intense winters, and a short exterior construction season. Those factors made an alternative approach to design and construction both necessary—and ideal.
In this exclusive interview, we spoke with architect Suresh Perera to learn more about the project.

Modular building vs. traditional construction
Canadian Architect: Can you explain how the mass-timber modules fit together to create the finished building, and why you feel this was the right approach in this situation?
Perera: For this project, mass-timber and modular are intrinsically linked. Continuous cross-laminated-timber (CLT) panels make up the walls, floors and ceilings of each module. This CLT shell is the core concept and forms both the structural and architectural components—it is self-supporting, inherently fire-resistant (without needing interior gypsum finishing, for example) and forms an interior vapour barrier.
Each module is, in many ways, a mini-building. Two linked modules become an apartment. The corridors, stairs and elevator are their own modules, which is important in order to avoid sound transmission.
These “mini-buildings” were individually constructed in a factory setting, and were then assembled into one complex system on site. An apartment building is essentially a collection of smaller repeated units, without large spaces or high ceilings, and is a perfect candidate for a modular building—especially in this case, considering all the constraints of building in the North. Being close to the factory and the source of the wood made the CLT construction an even more sustainable choice.
CA: From an on-site perspective, when you’re assembling the project, what are some of the big differences between this type of modular structure and a more traditional approach?
Perera: The construction of each module—each mini-building—occurred in a controlled factory environment and included the installation of doors and windows, exterior cladding, interior finishes, electrical and plumbing fixtures, and millwork. This process continued for many months over the winter and spring. The foundations were poured in early summer and, within just four incredible days, the modules arrived on trailers and were hoisted into place. The roofing joints were sealed, making the building waterproof.
The advantages are obvious. Not only are site-related weather issues no longer a problem, the factory fabrication allows for a high level of control, easy inspection and testing of systems, and safe working conditions, as the modules are always only one floor high.

Working relationships and factory fabrication
CA: How did you and your relatively small Montreal-based firm end up working with Nordic Structures on a project in such a remote northern city?
Perera: A few years ago, Nordic Structures was looking to build modular mass-timber classroom additions to schools. They approached
us to help develop the concept, as we had relevant experience with institutional projects. What started out as simple one-storey additions eventually led to more complex two-storey structures, where fire and acoustic separations and stair modules had to be carefully considered.
These projects were very successful—not only because of their technical efficiency, but also because the CLT product allowed us to leave the wood structure exposed on the interior, making the classrooms very attractive learning spaces.
Based on these early experiences with modular CLT construction and our experience with various scales of residential projects, it seemed a perfect next step to work on this building. Certainly, working on a project so remote posed many challenges!
CA: Working on a project so far away, with so many different people involved, sounds like it could be a major headache. Can you describe the working relationships that evolved as the project got underway? How complicated was it for you to work with a remote fabrication site?
Perera: Being a design-build collaboration, the entire process was different from a traditional design process. Strangely, the process also coincided with the pandemic, when remote work came into its own. Right from the very beginning of the early design stages, we had daily—and often more than just once-a-day—video-conference meetings and phone calls with the factory fabrication team at Chantiers Chibougamau and the engineers at Nordic, to work through design questions and details.
It was a huge learning curve for us, and for them as well. Not a single detail was standard, and we had to understand the factory fabrication sequence, limitations, and how to detail CLT structures from an architectural point of view. The engineering was inseparable from the architecture, and so, as our drawings developed, so did the engineering drawings.
There were ten distinct types of modules. We would physically visit the factory at the start of the construction of each type to ensure a complete coordination, and to make adjustments to the details and drawings as necessary. In some ways, the drawings were only complete at the end of the building process!
Nordic Structure’s engineers and the team at Chantiers Chibougamau were extremely dedicated throughout, and had a high understanding of their product and the process. Given that the entire approach was new to us, we relied on them as much as they did on us, to guide the process.
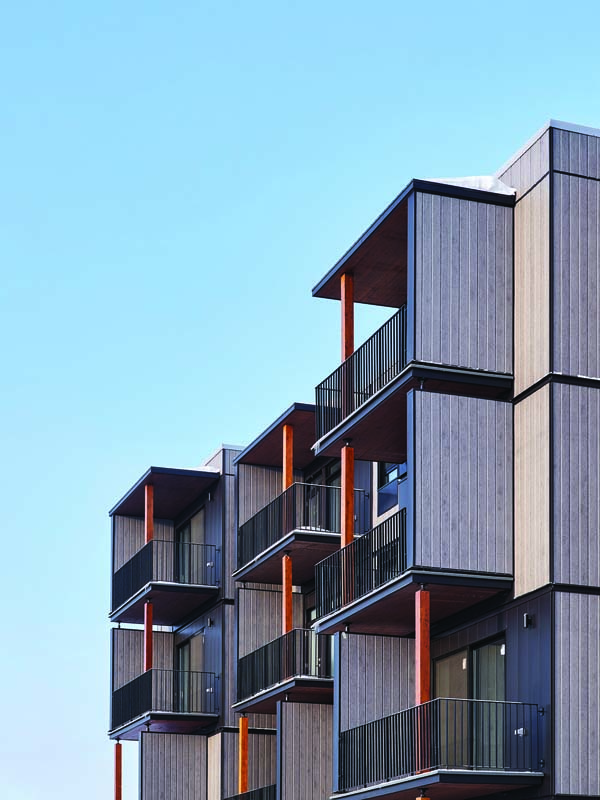
Architectural and technical design aspects
CA: Can we talk about some of the specific architectural and design challenges related to the project? How did your approach to the design manage to overcome these—and turn them into advantages?
Perera: Factory fabrication means the completed modules are limited in height and width due to the limitations of transporting them by road. However, using CLT panels means the wall, floor and roof compositions could be comparatively thin. We worked closely with the fabrication team to achieve the maximum height possible.
Our interior finished ceiling was 8’-9”. By combining several modules, we were able to get living space widths of 14.5 feet and bedroom widths of 12 feet, which compares favourably with traditional apartment building sizes.
The CLT shell had other benefits, such as a highly thermally efficient structure in comparison to wood-frame. We strongly felt that the wood should be exposed on the interior, and we picked certain areas to do so, including the ceilings, certain accent walls in the units, and the walls of the staircases. The big advantage is that the CLT plays multiple roles—structural, technical and architectural—thereby reducing the total material consumption while creating warm, aesthetically pleasing interior spaces.
CA: From the viewpoint of aesthetics, modular buildings have a reputation of being quite repetitive and banal, with minimal architectural opportunities. “Generic” is a word that’s plagued the modular approach. How did you flip this impression and create a building worth talking about?
Perera: Modular construction becomes most cost-effective by repeating identical components, which often leads to monotonous and flat buildings with small openings. The concept here was to find visual shifts and variations within repetition that did not reduce structural or construction efficiency. Shifting window positions in modules that were identical on the interior reduced the monolithic aspect of the building, as did pulling in and pushing out adjacent modules.
We also worked closely with the structural team to create large balconies that appear to flip and shift on the façade, but are identically attached to each module, in order to standardize construction. Likewise, we worked with the structural team to have large windows in the living spaces that provide ample natural light and animate the façade. The structural capabilities of the CLT also allowed for open interior living spaces without the need for columns, structural division, or large structural members.
CA: Sounds like the materials used in this project really allowed you to push the conventional understanding of what modular structures can be from a design perspective. How did the technical aspects of working on this project compare to standard construction methods?
Perera: An important challenge was resolving some of the acoustical and fire safety details within the construction—especially dealing with construction voids, points of contact between the modules, and the passage of electrical and mechanical building services. The other significant challenge was understanding how to deal with differential movement between the modules over time, and how to maintain accessibility for people using mobility devices. The building is a prototype in many ways, and will continue to be monitored over time, as part of a project between Nordic Structures and FPInnovations.
How to configure and build certain modules was another challenge. The entire stair shaft, for example, was a single module, for several reasons, including fire resistance. It was built horizontally—including the installation of the staircase—and then installed on site vertically.
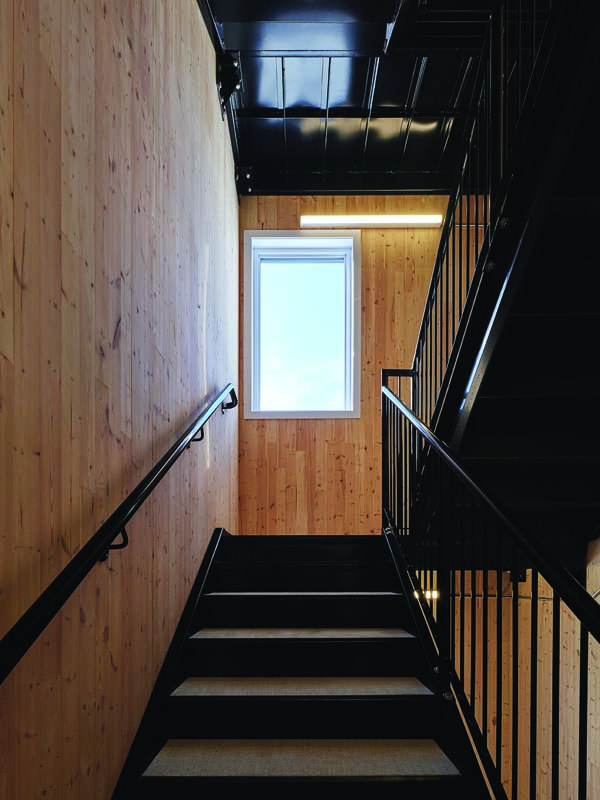
CA: Wood construction is usually considered far inferior to a material such as concrete when it comes to acoustics and fire resistance—important elements when designing a multi-unit building like this. Can you discuss how you were able to use wood so effectively in this project?
Perera: We worked closely with acoustical experts and testing companies to evaluate wall, floor and inter-module compositions, shifting the design and detailing to respond to the results.
Conceptually, the idea was to structurally separate the residential units from each other and from the public spaces. The modular system of construction allowed us to do this, as each apartment had its own shell—its own floors, walls and ceiling—separate from adjacent units. The corridors were their own modules. There are no attachments tying the modules together, removing a major weakness that causes sound transmission. Each module simply rests on the module below, with acoustic pads to separate them. The tested STC and IIC values were well above the building code requirements.
The CLT panels have an inherent fire resistance, making it a much more effective building material for fire resistive assemblies than, say, wood frame construction.
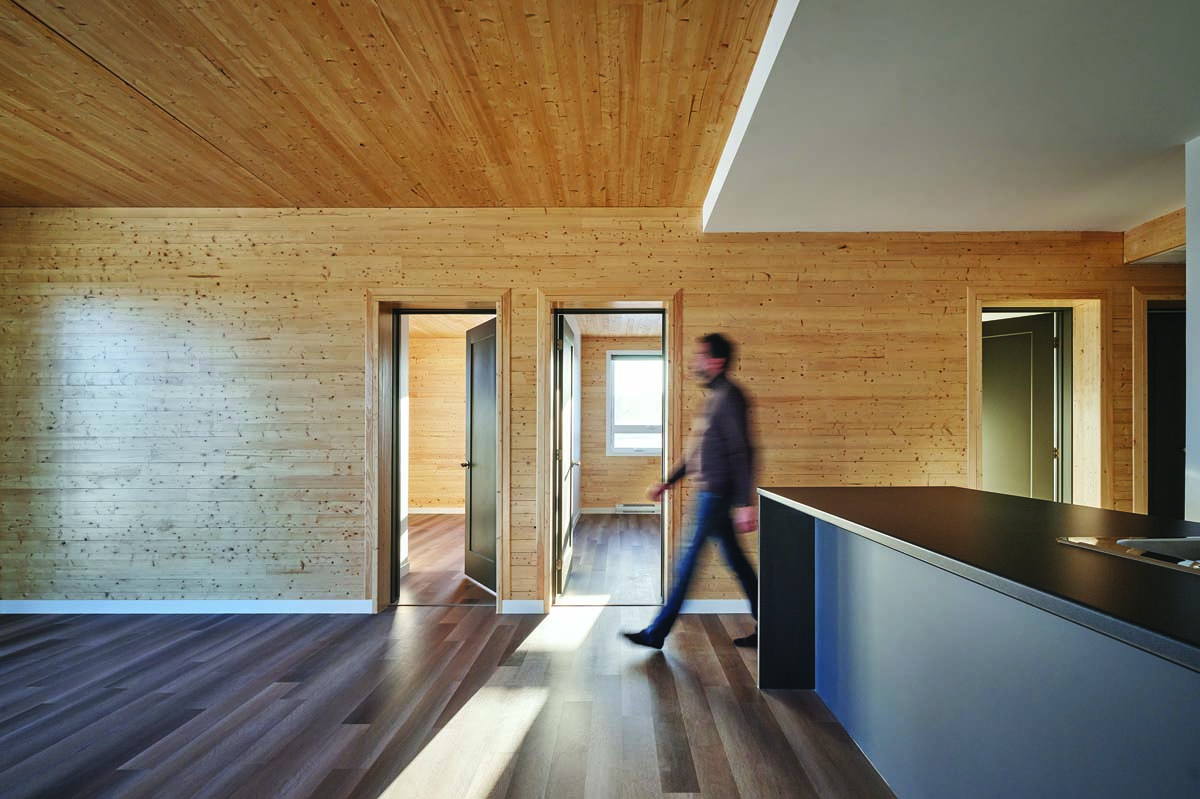
Sustainability
CA: Sustainability has evolved to become the foundation of so many projects in the past decades. How does Les Pavillons du 49° fit into this approach to building? How does it move the concept forward?
Perera: It’s estimated that the 987 cubic metres of wood used in this project is grown in US and Canadian forests in three minutes. With the stored carbon and avoided greenhouse gases, it’s easy to argue for the benefits of mass-timber versus, say, concrete or steel construction. But each module still has its own floor and ceiling, and though this is great from a sound transmission and fire resistance point of view, it also means more wood is used compared to a typical wood-frame construction. I believe there’s still room for an improved efficiency of construction. We are still searching for that perfect balance of responding to needs and working within construction limitations, while achieving minimal material and energy use.
This being said, the higher density achieved by the mid-rise compared to the typical North American neighbourhood of single-family homes is great in terms of minimizing urban sprawl and dealing with deforestation in this type of ecosystem. Especially in light of last year’s fire season—which saw Chibougamau evacuated as forest fires approached the city—the need to be conscious of the fragility of this ecosystem seems more urgent than ever.
Marco Marini is an architect with Figurr who works extensively on projects located in Quebec’s north.
CLIENT L’OBNL des Pavillons du 49 | ARCHITECT TEAM Suresh Perera, Julie Charbonneau | STRUCTURAL Nordic Structures | MECHANICAL/ELECTRICAL UNIGEC | CONTRACTOR & MODULAR FABRICATION Chantiers Chibougamau | AREA 2,275 m2 | BUDGET Withheld | COMPLETION January 2024
As appeared in the April 2024 issue of Canadian Architect magazine