Spreading the Wood: Three projects that are leading the way in Canadian mass timber innovation
A look at the latest mass timber innovations by Michael Green Architecture, Moriyama Teshima Architects, Acton Ostry Architects, and Intelligent City.
Over the past decade, engineered mass timber has evolved from a new and innovative choice of structural material to becoming almost mainstream. Canadian architects have played a major role in the material’s acceptance in the North American building industry, with British Columbia architects at the vanguard of harnessing Cross-Laminated Timber (CLT) around 10 years ago.
As the three in-construction projects featured on the following pages demonstrate, Canadian mass timber expertise continues to advance—and in Michael Green’s case, it is garnering international projects. Moreover, architects including MTA with Acton Ostry are looking beyond the material’s vaunted renewability and carbon-sink aspects to make their mass-timber buildings even more environmentally sound. And lastly, architects like Intelligent City are integrating and overhauling the very process of designing and building with mass timber.
The material choice still requires something of a helping hand in terms of subsidies and investment. Though few architects speak freely about it, choosing an engineered wood structure is usually a more expensive way to build—at least for the moment. But that could change quickly as the immense carbon costs of construction become reflected in pricing and in regulations. And as more innovative and impressive projects near completion and prove their mettle, Canadian architects will continue to show that they remain at the forefront of mass timber innovation.
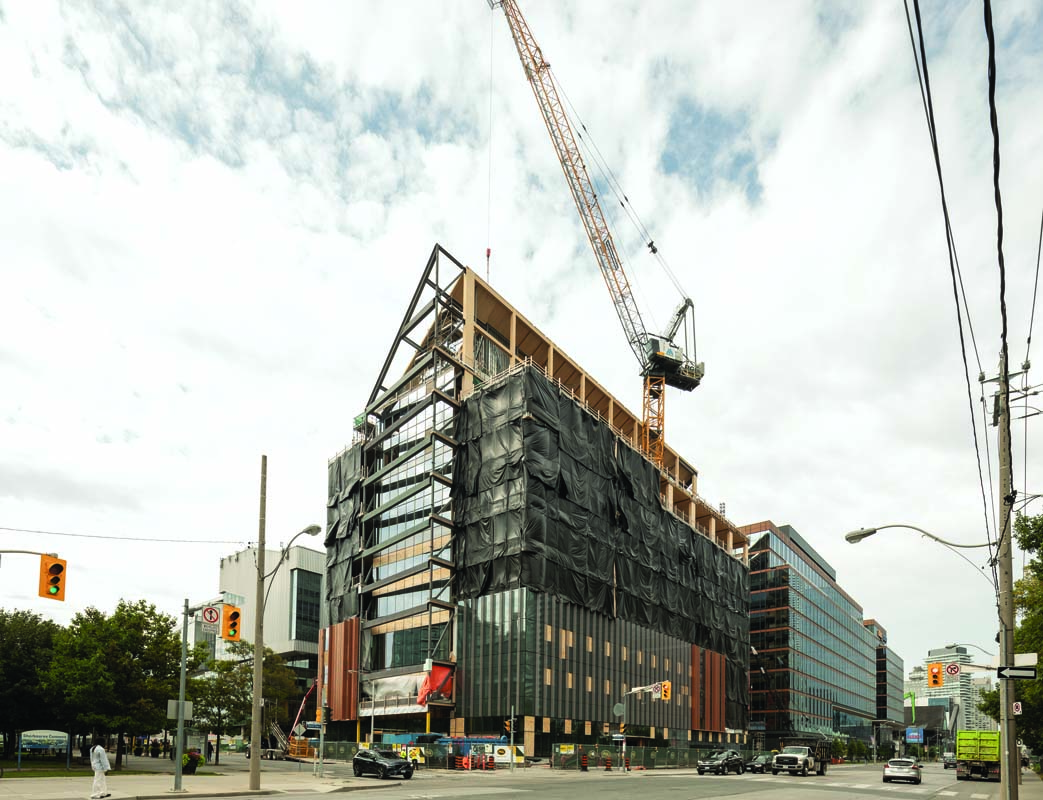
Limberlost Place
An innovative structural system and pre-fabricated envelope set new standards for mass timber public buildings.
LOCATION George Brown College, Toronto, Ontario
ARCHITECTS Moriyama Teshima Architects + Acton Ostry Architects
Even while still under construction, Limberlost Place is hauling in acclaim. Part of George Brown College’s waterfront campus in Toronto, the building has pulled in over a dozen awards, including the RAIC’s 2023 Research & Innovation in Architecture Award, and a Canadian Architect Award of Excellence. Expect more accolades upon its projected completion in January of 2025.
At 10 storeys high, Limberlost Place is one of the world’s tallest mass-timber institutional buildings. Buildings of this typology must meet onerous construction codes and design considerations; this one will serve 3,400 students and staff. Teaching and gathering spaces occupy the full structure, including a tall-wood research institute, childcare centre, classrooms, and areas for lounging and study. MTA’s Vancouver-based joint-venture partner, Acton Ostry Architects, has already established a benchmark in designing the 18-storey Brock Commons Tower at the University of British Columbia, at the time the tallest mass-timber project in the world.
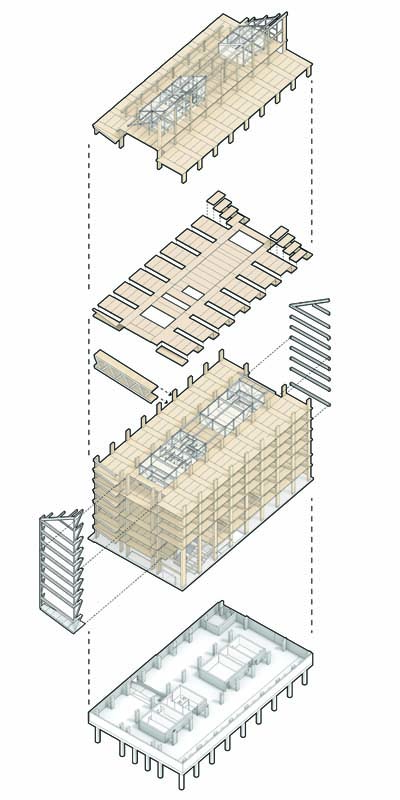
Like Brock Commons, Limberlost Place is a hybrid structure of CLT, concrete, and steel. But where Brock Commons’ CLT was mostly hidden under drywall, roughly 50 per cent of Limberlost’s is exposed to view, including its nine-metre-span beams and every column in the building. Its 10-storey height clocks in four storeys above the conventional pre-CLT code, “so we had to be meticulous about every element,” says MTA principal Phil Silverstein, who is the construction administration lead on the project.
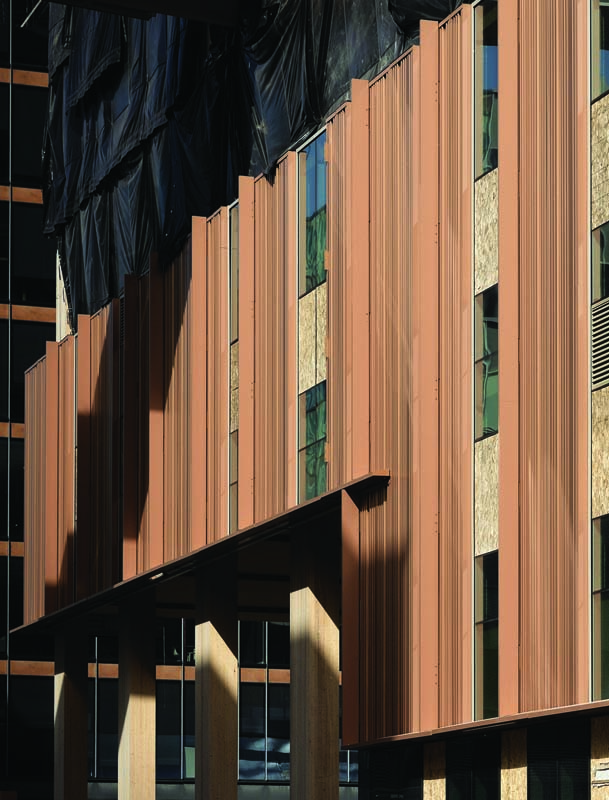
While many North American mass-timber structures are still sourced from overseas suppliers, Limberlost has taken a made-in-Canada approach. Its prefabricated envelope system arrived in two-storey panels assembled in Windsor, Ontario, and delivered just-in-time to eliminate on-site storage needs. The prefab wall panels have been manufactured up to 11.7 metres high and are quickly assembled on site and supported by jack posts. The CLT for Limberlost Place—manufactured largely from fast-growing black spruce—comes from Quebec-based Nordic Structures.
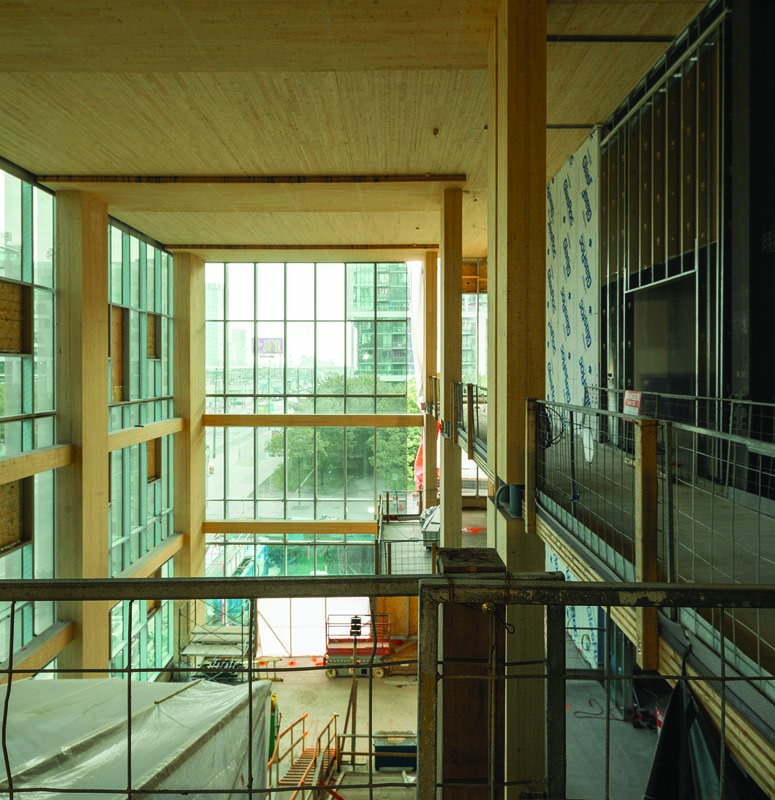
As we walked through Limberlost mid-construction, we could already sense the dramatical verticality of its interior, dominated by a three-storey-high glazed foyer connected to smaller common spaces—“breathing rooms,” as design partner Carol Phillips calls them—on the second and third levels. The open volume of the foyer is anchored by a 16-metre-high glulam column, the heaviest member of the entire project, weighing in at 22,000 pounds. “Timber doesn’t like to transfer loads very well,” notes Silverstein. “Timber likes to work vertically.”
In horizontal terms, a major innovation is the ultra-generous 9.2-metre span of the teaching spaces. It’s essentially a “beamless” construction system: its main structural member is a timber-concrete slab band, composed mostly of CLT, topped by a layer of reinforced concrete. “It’s an extremely shallow system,” notes Phillips, allowing for greater floor-to-ceiling heights as well as column-free spaces ideal for large-group instruction.
The building has environmental attributes well beyond its use of mass timber. Solar chimneys on the east and west façades will draw air up and through the building from operable windows, to harness the stack effect and establish a natural convection system for temperature regulation. The building informally meets Passive House standards and meets the energy targets for LEED Platinum status, according to the architects, although they will apply for LEED Gold.
The most salient value of the project is that it will provide a paradigm for many more sustainable mass-timber public buildings in the future. “This isn’t a one-off,” says Silverstein. “It’s a starting point.”
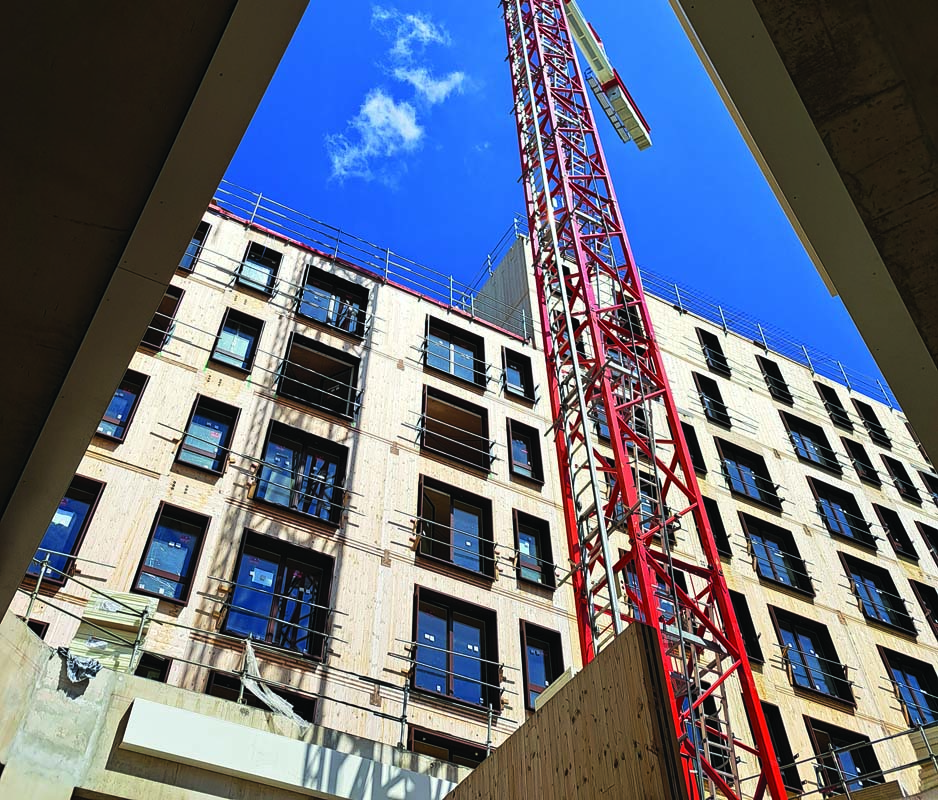
Flora
Canadian mass timber expertise is being tapped for this project in Europe.
LOCATION Nanterre, France
ARCHITECTS MGA | Michael Green Architecture + CALQ Agence d’Architecture
The first thing you notice about Flora is the sensuality of its form. Even in mid-construction, its rounded corners, jogged massing, and prow-like base distinguish it from the other rectilinear buildings around it. Its principal designer, Michael Green, avers that the building’s voluptuous shape is entirely logic-based, following the irregularities of the site and the material economy of avoiding 90-degree corners that often end up as wasteful underused space.
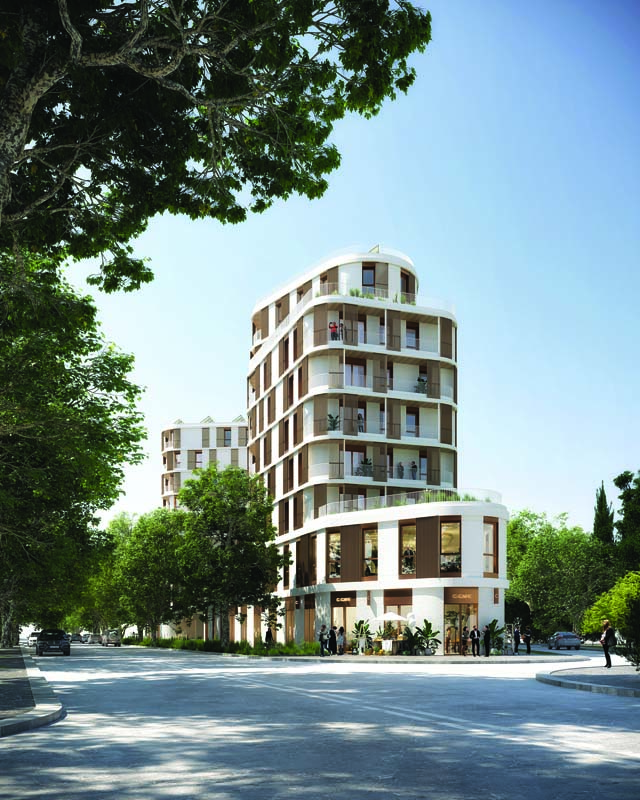
Flora is a nine-storey mixed-use complex, with offices and retail slated for the lower floors, and a mix of market and non-market housing above. Here in Nanterre, a fast-growing suburb of Paris, Green has teamed up with local architecture firm CALQ Agence d’Architecture to bring his knowledge, design, and powers of persuasion to France. CALQ’s website states that the firm’s main reason for using mass timber is to combat “le réchauffement climatique.” Green concurs. And Woodeum, the Paris-based real-estate developer and the project’s client, promotes itself as a specialist in low-carbon wood architecture—making Canada’s best-known mass-timber advocate a natural choice for a partnership.
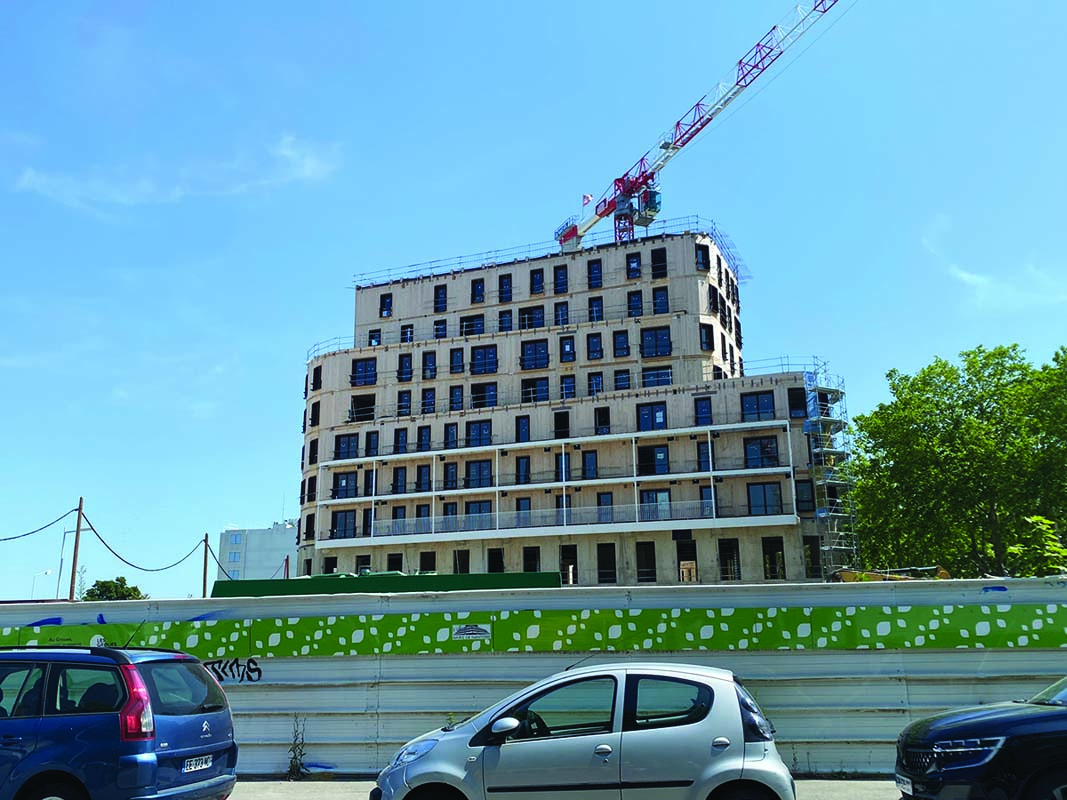
This summer, as Green surveyed the busy construction site in person for the first time, he noted some of the distinctions between building in France versus in his homeland. For instance, the interior of Flora is enlivened by a spiral staircase—a charming, fun, and space-saving element. In Canada, the building codes disallow spiral staircases, because they are allegedly dangerous—although, as with so much in life, risk calibration is partly a subjective matter.
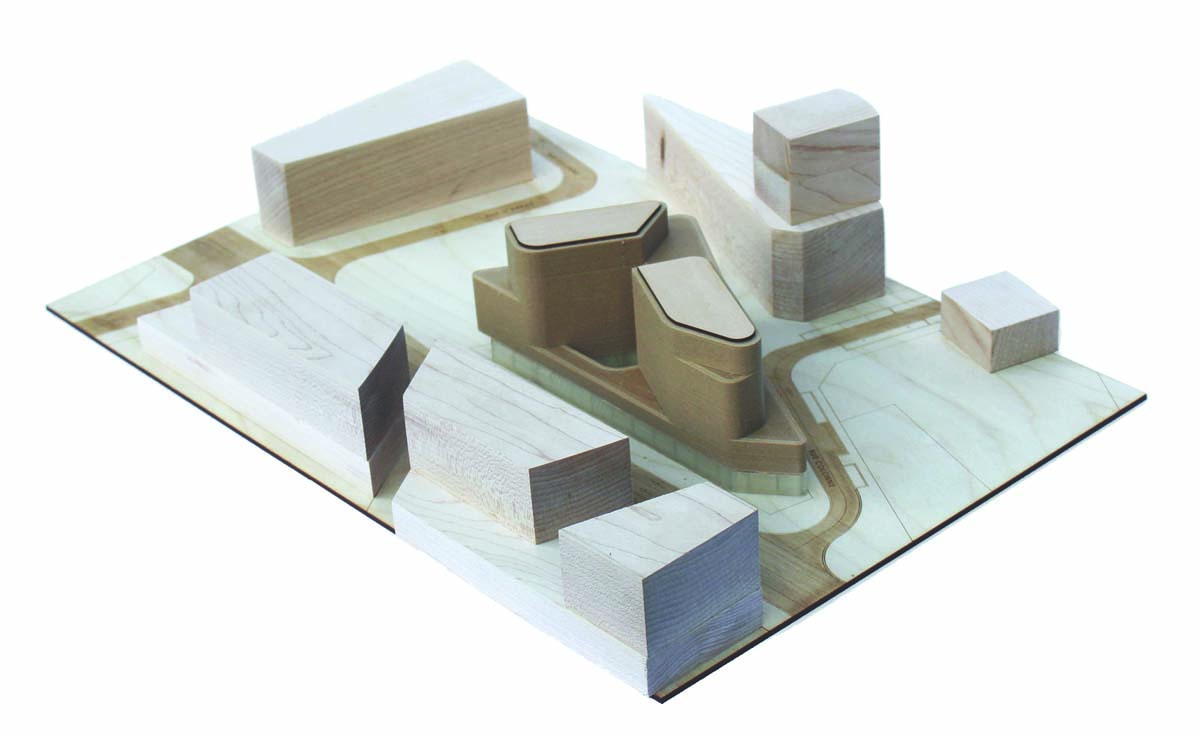
Although the French remain détendu about risks that furrow the brows of Canadian code-writers, they are rigorous about certain other requirements that enhance sustainability and quality of life, notes Green. Their national building code includes the stipulation for cross-ventilation, for instance, while our national building code has nothing of the sort for residential construction.
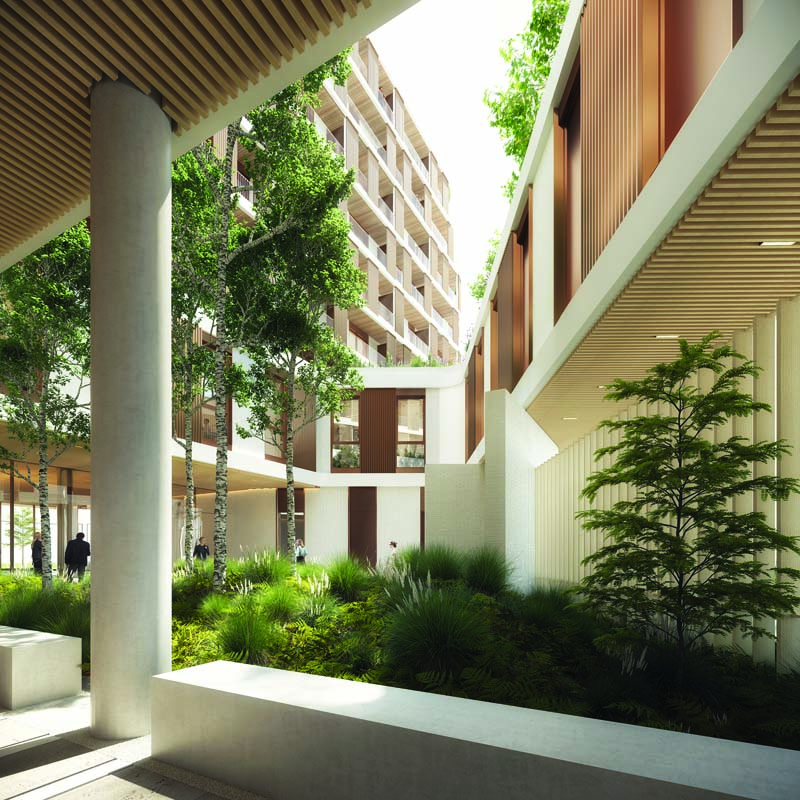
In Green’s most recent TED Talk, he unpacked his bid for the next big transition in mass-timber engineering and design: a system based on biomimicry. He foresees a future of plant-based materials whose lignified tissues and cellulose are reinforced in a way that will allow the architecture to carry loads in the same way as tree branches, with an aesthetically pleasing curvilinearity that would have an inherent structural logic. And instead of the standard spruce-fir-pine now used for most Canadian mass timber, the choice of plant will be based on what’s local and ecologically appropriate. “It might be bamboo in one region, and then grass, or salal, or hemp in another,” he says. His concept “is going to be a big thing. It’s not happening yet, but it will in ten, twenty years,” he avows. “As humans, we’re very resistant to the idea of starting over. But we need to rethink all aspects of the built environment.”
Back to the here and now: French authorities, like their North American counterparts, are still nervous about transitioning the entire structural framework of buildings to mass timber. That’s not the way Green would have it. The ground floor of Flora is concrete, and so it’s essentially a hybrid structure. All over the world, including here in Canada, notes Green, “concrete use is driven largely by code. So, you have different trades, you have two different structural materials, you have finger-pointing.” It’s not the cheapest or the most efficient way of building, but it will change, he expects, or at least hopes. “We’re still stuck in a version of the old system. It’s time to move on.”
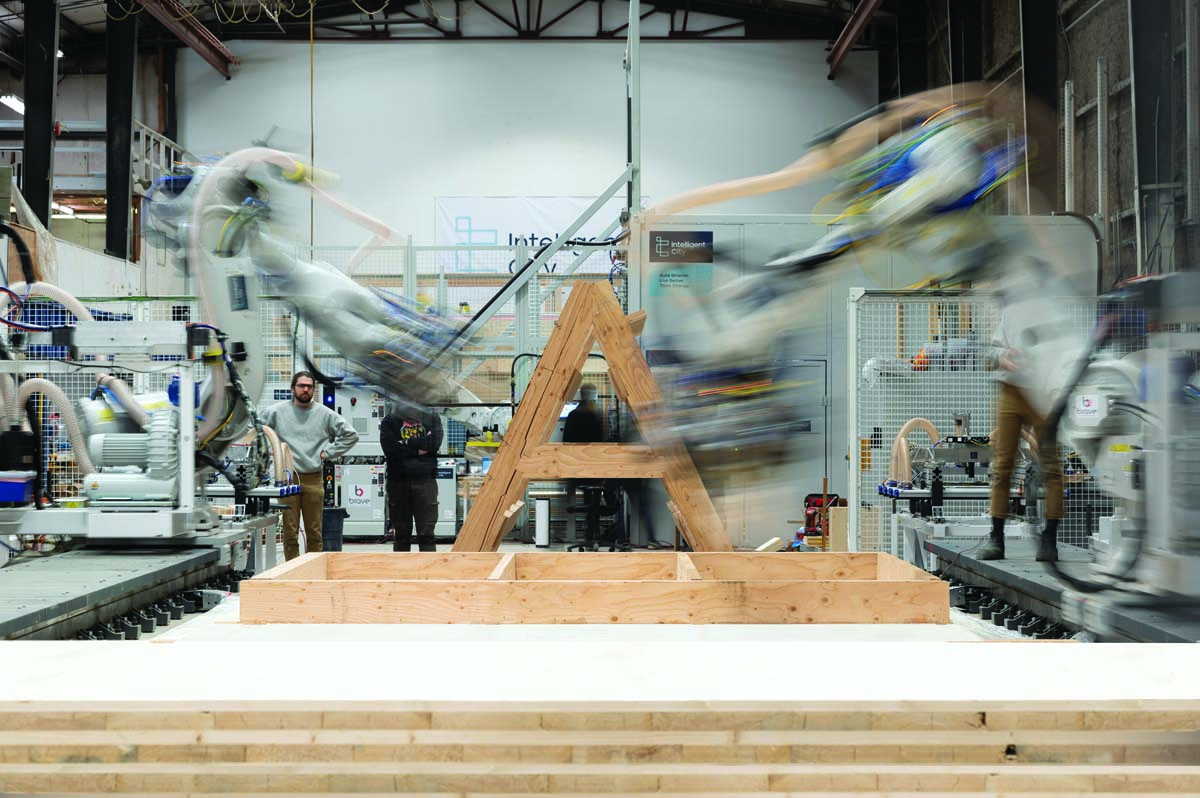
Intelligent City
An integrated system of design and manufacturing is the project.
LOCATION Delta, British Columbia
In some ways, the Intelligent City factory in Delta, B.C., seems like some sort of sci-fi film set. A giant robot lumbers around in a caged space, looking oddly like a Meccano dinosaur. And yet this metallic creature may well be the future master builder of the region. Controlled by a petite woman holding what looks like a PlayStation remote-control device, the robot is building mass timber components for the firm’s first real-world project.
“We saw that the delivery of infill urban housing—multi-housing in particular—was difficult to develop,” says Cindy Wilson, the company’s co-founder with architect Oliver Lang. “Every time you have a new person come to a team, they have their own way of thinking how things should be done. So how could we curate a system that is more integrated and could be repeated at scale?”
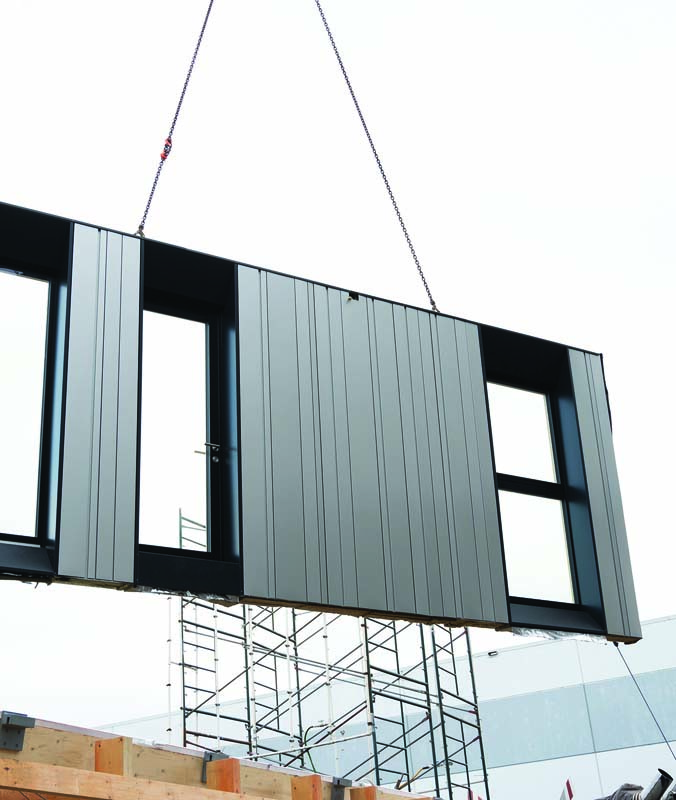
By unifying and distilling the messy process of construction into software-controlled prefabrication, the firm essentially smooths over the schism between design and manufacturing, and streamlines the custom design work that is usually dedicated to discrete buildings. Since the Intelligent City team has more control of the overall process, they can also ensure more price stability. This was evidenced in one of their current projects. “During Covid, the price of construction almost doubled,” notes Wilson. “But importantly, about 60% to 80% of a building’s superstructure is our components, so those prices remained stable. We’ve also developed an ecosystem of a supply chain.”
As previously reported in Canadian Architect, Intelligent City—the sister firm of Lang Wilson Practice in Architecture Culture (LWPAC)—opened its manufacturing facility in Delta, B.C., two years ago. Now the factory is thrumming as its staff and ultra-high-tech software produce the largely pre-assembled components for the “product proof,” a kind of miniature sample building that staff work on to determine where and how the components will later be assembled on-site.
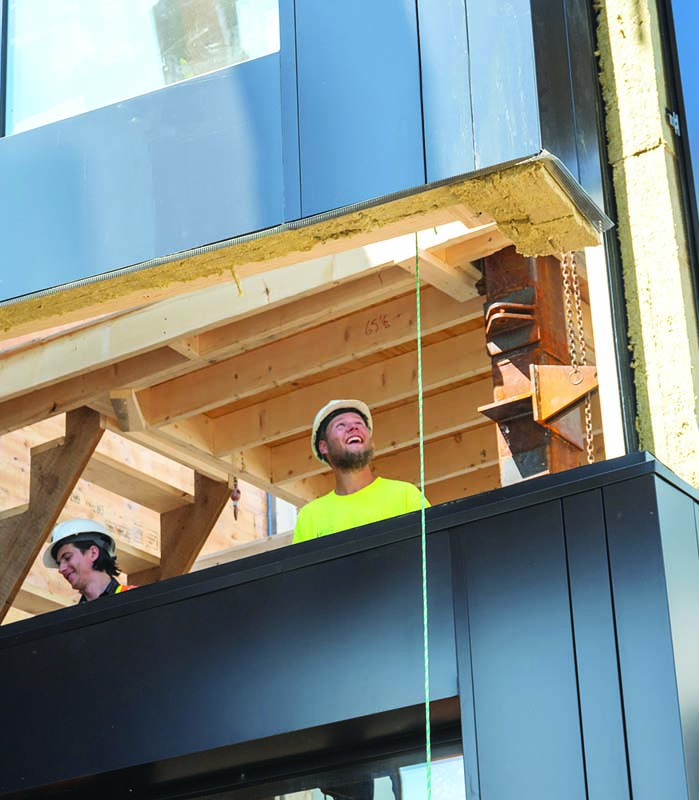
The firm’s first “real-world” building will be the Vancouver Native Housing Society’s Khupkhahpay’ay Building, a nine-storey housing project to be built in East Vancouver by GBL Architects and Ventura Construction Corporation. Intelligent City is producing the building’s Passive-House façade system.
The two-year period from factory inception to the launch of actual construction reflects the typical process of testing, commissioning and certification of the building systems and the robotics, but this first real-world project will smooth the way for more projects, built faster, says Wilson. To create a system that would not only be repeatable and scalable but also customizable, the Intelligent City team has streamlined the entire process of building, from preliminary design to construction, so that design and manufacturing are integrated from the start. The fruits of this work are most impressive at the end stages: remote-controlled with proprietary software, the factory’s giant robot lifts, positions, and custom-cuts oversized panels of mass-timber walls, floors, and ceilings. The cuts are unique to each product and can vary in size and shape, allowing electrical channels and ventilation ducts to be embedded in the components before they even leave the factory. Crucially, the customization is instantly and economically adjusted for each component and each project by altering the instructions to the robot.
The result is a convergence of two processes—architecture and construction—that are normally sequential, separate, and rarely align as well as we’d like them to. There is usually no downtime from delays in material delivery or labour shortages. Once on-site, the components will be assembled much more rapidly than in conventional on-site construction, with much of the electrical and ventilation elements already embedded in the structural framework.
Wilson and Lang believe that Intelligent City’s approach will have an impact not only on the take-up of climate-friendly mass timber, but also in addressing the housing affordability crisis. “The more control we have over the building, the more we can control costs,” says Wilson. “This is where we can really make a difference in affordable housing. It’s not just time, materials, or labour. It’s how we can roll out the creation of housing at scale, in a systematic, predictable way.”